Duro-Sense Corporation provides the precision temperature sensors to the aerospace, aviation, and space industries. Duro-Sense engineers bring proven solutions to your most difficult problems. Their R&D department is staffed with some of the industry's most qualified people, working in the most modern facilities to help advance the state of the art in temperature measurement.
A blog providing information about industrial temperature measurement, specifically in the areas of temperature sensors. The posts will contain educational information about thermocouples, RTDs, and other common types of temperature sensors. The application of these sensors will focus on aerospace, aircraft, research and development, medical, chemical, plastics processing, and power generation industries. For more, visit Duro-Sense.com or call 310-533-6877.
Friday, February 15, 2019
Temperature Sensing IS Rocket Science
Duro-Sense Corporation provides the precision temperature sensors to the aerospace, aviation, and space industries. Duro-Sense engineers bring proven solutions to your most difficult problems. Their R&D department is staffed with some of the industry's most qualified people, working in the most modern facilities to help advance the state of the art in temperature measurement.
Thursday, January 31, 2019
Thermocouples
![]() |
Diagram of a thermocouple circuit. |
![]() |
Typical sheathed thermocouple. |
Because of their wide range of models and technical specifications, it is extremely important to understand their basic structure, functionality and range in order to better determine the right thermocouple type and material for an application.
Operating Principle
When two wires consisting of different metals are connected at both ends and one end is heated, a continuous current flows through the thermoelectric circuit. If this circuit is broken in the center, the net open circuit voltage (Seebeck Effect) depends on the temperature of the junction and the composition of the two metals. This means that a voltage is produced when the connection of the two metals is heated or cooled that can be correlated to the temperature.
Contact Duro-Sense Corporation with any questions about applying industrial and commercial thermocouples.
Duro-Sense Corporation
https://duro-sense.com
310-533-6877
Monday, January 28, 2019
Where to Mount Industrial Temperature Transmitters?
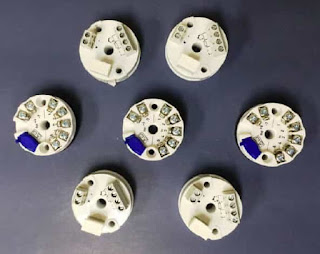
There are basically three different locations for the mounting of the temperature transmitters:
- In-head mounting - inside the connection head of the temperature sensors.
- Field mounting – close to the temperature sensors.
- Central mounting - in the vicinity of the control room
In-head mounting
The transmitters are mounted directly inside the connection head and are normally replacing the terminal block. This way of mounting normally offers the biggest advantages. It is however necessary to be aware of the environmental influence (mainly the temperature) on the measurement accuracy.Advantages
- Maximum safety in the signal transmission. The amplified signal, e.g. 4- 20 mA, is very insensitive to electrical disturbances being induced along the transmission cable.
- Cost savings for the transmission cables. Only two leads are required if a 2- wire transmitter is used.
- Cost savings for installation. No extra connection points because of the transmitter.
- Cost and space savings. No extra housings or cubicles are needed.
- Field instruments, e.g. indicators, can easily be installed, also at a later stage without redesigning the measuring circuits.
- The ambient temperatures can be out- side the allowed limits for the transmitters.
- The ambient temperature influence on the measuring accuracy has to be considered.
- Extreme vibrations might cause malfunction of the transmitters.
- The location of the temperature sensor can give maintenance problems.
Field mounting
The transmitters are either mounted directly beside the temperature sensors or in the vicinity of the sensors. Often more than one transmitter is mounted in the same field box.This method is more expensive than In-head mounting, but otherwise a good alternative offering most of the advantages of In-head mounting without the disadvantages mentioned above.
Advantages
- High safety in the signal transmission. The main part of the signal transmission is made with an amplified signal.
- No extreme temperatures or vibrations exist. This facilitates accurate and safe measurements.
- Cost savings for transmission cables.
- A wider selection of transmitters is available. DIN rail transmitters can also be used.Field instruments can often be installed easily.
- Maintenance can normally be carried out without problems.
- Higher installation costs compared to In-head mounting.
- Costs and space requirements for transmitter boxes or cubicles.
Central mounting
In this case, the transmitters are placed in the vicinity of the control room or in another central part of the plant They are often mounted inside cubicles, and/or closed rooms. The ambient conditions are normally very good and stable.This method offers the most convenient conditions for maintenance and the best possible environment for the transmitters. There are on the other hand some disadvantages that should be considered.
Advantages
- Convenient conditions for installation, commissioning and maintenance.
- Minimum risk for environmental influences (e.g. temperature influence).
- Reduced safety in the signal transmission. The low-level sensor signal is rather sensitive to electrical disturbances being induced along the trans- mission cable.
- Relatively high costs for cabling. T/C measurements require compensation or extension cables all the way to the transmitters. RTD measurements with high accuracy should be done in 4-wire connection to get rid of the lead resistance influence.
- Costs and space requirements for cubicles or frames.
- Rather complicated and expensive to connect field instruments, e.g. indicators.
For more information on using temperature transmitters, contact Duro-Sense by calling 310-533-6877 or by visiting https://duro-sense.com.
Wednesday, January 16, 2019
Sunday, December 30, 2018
Wednesday, December 12, 2018
Happy Holidays from Duro-Sense!
From all of us at Duro-Sense, we wish our customers, partners and vendors a safe and happy holiday season and a wonderful 2019!
Monday, December 10, 2018
Duro-Sense a Critical Partner in Hydrogen Contamination Detector
We take for granted the gasoline (or diesel) we put in our cars and trucks is free from contaminants when pumped in to our gas tanks. The purity we've come to expect at the fuel pump didn't happen overnight. It took many years, and thousands of engineering hours, to develop the refining processes that produces today's clean gasoline and diesel.
Fuel Cell Vehicles are a category of electric vehicle (EV's). Fuel cell vehicles use hydrogen gas (H2) to power an electric motor. Unlike conventional vehicles which run on gasoline or diesel, fuel cell cars and trucks combine hydrogen and oxygen to produce electricity to drive the motor.
Similar to the path that gasoline and diesel processing took toward purity, the use of H2 as feedstock for fuel cells in transportation has driven requirements for H2 purity standards to very strict levels. This push has also elevated the need for cost-effective and reliable instruments that can sample H2 near the nozzle of a delivery pump, and either certify acceptability or provide a signal to shut off the fuel distribution system.
Duro-Sense Corporation, a California based manufacturer of high quality temperature sensors, is part of a team working under a DOE funded research program to develop a Hydrogen Contamination Detector. The sensor, which will be installed at hydrogen fueling stations, will detect poor quality hydrogen gas before entering the fuel cell vehicle. The sensor is intended to detect multiple impurities at extremely low levels in hydrogen to prevent fuel cell performance degradation.
Duro-Sense is designated as the industrial partner and vendor aiding in defining the commercial manufacturability of the Hydrogen Contamination Detector.
As part of their preliminary work, a thermocouple embodiment was selected as a cost-effective platform for the Hydrogen Contamination Detector because:
- Direct Commercial Availability
- Proven History of Reliability and Robustness
- Adaptability of Conductor Materials for Most
- Appropriate Catalyst for Each Contaminant
- Ability to Incorporate up to 12 Conductors a Single Thermocouple, Reducing Fluid Stream Penetrations
The Hydrogen Contamination Detector project is still in its very early stages, and research and development continues, subject to funding and continued interest in alternative fuel technology.
For more information, contact Duro-Sense at 310-533-6877 of visit their web site at https://duro-sense.com.
Subscribe to:
Posts (Atom)