A blog providing information about industrial temperature measurement, specifically in the areas of temperature sensors. The posts will contain educational information about thermocouples, RTDs, and other common types of temperature sensors. The application of these sensors will focus on aerospace, aircraft, research and development, medical, chemical, plastics processing, and power generation industries. For more, visit Duro-Sense.com or call 310-533-6877.
Friday, May 24, 2019
Quick Comparison of Temperature Sensors
Thermocouples are commonly used because of their simplicity, reliability, and relative low cost. They are self-powered and eliminate the need for a separate sensor power supply. Thermocouples are quite durable when selected for a given application appropriately. Thermocouples can also be used for applications with high temperatures.
Resistance temperature detectors (RTDs) are attractive alternatives to thermocouples when the output is desired to be highly accurate, stable and linear (i.e. just how close the calibration curve looks a straight line). The superior linearity of relative temperature resistance enables simpler signal processing devices for RTDs than thermocouples.
Thermistors are similar to RTD because they're a resistance measurement device, but thermistors use a very cheap polymer or ceramic material as the element in lieu of the use of pure metal.
For more information on any type of industrial or OEM temperature sensor, contact Duro-Sense by calling 310-533-6877 or by visiting https://duro-sense.com.
Labels:
industrial thermocouple,
OEM,
RTD,
temperature sensor,
thermistor,
thermocouple
Wednesday, April 24, 2019
Friday, April 19, 2019
Thermocouples: Proper Use, Recommended Practices, and Avoiding Problems
![]() |
Proper use and maintenance of thermocouple systems begin with good system design based on the strengths and weaknesses of various thermocouple types. Because these sensors contain sensitive electronics, general good practice includes use of shielded cases and twisted- pair wire, use of proper sheathing, avoidance of steep temperature gradients, use of large-gauge extension wire, and use of guarded integrating voltmeters or ohmmeters, which electronically filter out unwanted signals. The signal conditioner should be located as close as possible to the sensor, and twisted copper-wire pairs should be used to transmit the signal to the control station. To minimize electromagnetic field interference, sensor system wires should not be located parallel to power supply cables. The primary causes of loss of calibration in thermocouples include the following:
- Electric “noise” from nearby motors, electric furnaces, or other such electrically noisy equipment;
- Radio frequency interference from the use of hand-held radios near the instrument.
- “Ground loops” that result when condensation and corrosion ground the thermocouple and create a ground loop circuit with another ground connection in the sensing circuit.
Most problems with thermocouples are aggravated by use of the thermocouple to measure temperatures that approach or exceed their upper temperature limits. Careful recording of events that could affect measurements should be kept in a logbook. Any adjustments or calibrations should also be recorded. The logbook should contain the names of individuals performing maintenance and calibrations as well as defined procedures. In systems monitoring many locations, such a log is especially useful for fault diagnosis.
Thermocouples sometimes experience catastrophic failures, which may be preceded by extreme oscillations or erratic readings. In such cases, all connections associated with the thermocouple should be checked for loose screws, oxidation, and galvanic corrosion. In many cases, drift may be a more serious problem because it can go unnoticed for long periods of time. The most common causes of loss of calibration are excessive heat, work hardening, and contamination. Work hardening generally is due to excessive bending or vibration and can be prevented with properly designed thermowells, insertion lengths, and materials. Contamination is caused by chemicals and moisture, which sometimes attack wiring by penetrating sheaths, and can result in short-circuiting. A simple test to check for this problem is to disconnect the sensor at its closest connection and check for electrical continuity between the wires and the sheath using a multimeter. If the meter indicates continuity, the sensor should be replaced. Because the electromotive force (EMF) produced by thermocouples is so small, electrical noise can severely affect thermocouple performance. For that reason, it also is very important that transmitters be isolated. Thermocouples used in the vicinity of electrostatic precipitators must be shielded to avoid electrical interference. If the potential electrical interference is high, an RTD or other type of sensor may be preferred to thermocouples. With respect to thermocouple and protection tube selection, the following should be noted:
- Type J thermocouples particularly should not be used in applications in which they might be exposed to moisture because the iron in the thermocouple will rust and deteriorate quickly;
- Type K thermocouples should not be used in the presence of sulfur, which causes the element to corrode; because cutting oils often contain sulfur, protection tubes should be degreased before being used; stainless steel sheaths should be used to protect Type K thermocouples in stacks where SO2 emissions are significant;
- Platinum thermocouple elements (Types R, S, or B) should not be used with metal protection tubes unless the tubes have a ceramic lining because the metal will contaminate the platinum;
- Ceramic, silicon carbide, and composite (metal ceramic, Cerite-II, Cerite-III) protection tubes are subject to thermal shock and should be preheated prior to inserting in high temperature process environments; and
- Molybdenum - or tantalum-sheathed thermocouples will fail rapidly if placed in oxidizing atmospheres.
During one study of thermocouple performance, 24 combinations of thermocouple and sheath material types were tested at temperatures up to 1200 C (2200 F). The results indicated that above 600 C (1110 F) thermocouples are affected by complex chemical interactions between their components; even though wires and sheaths were physically separated, exchange of constituents occurred. The study concluded that thermocouples maintain calibration better if sheath material is similar in composition to thermocouple alloys. By using similar alloys longer performance can be expected for sensors subjected to temperatures above 600 C (1110 F), and the use of similar alloys is essential for temperatures above 1000 C (1830 F).
For more information on the proper use of thermocouples, contact Duro-Sense Corporation by calling (310) 533-6877 or visit their website at https://duro-sense.com.
Reprinted from CAM Technical Guidance Document courtesy of EPA.gov.
Sunday, March 31, 2019
Digital Food Thermometers: Thermocouples
![]() |
Specialized thermocouple, with handle and sharpened point, used in food preparation. |
A thermocouple measures temperature at the junction of two fine wires located in the tip of the probe. Thermocouples used in scientific laboratories have very thin probes, similar to hypodermic needles, while others may have a thickness of 1/16 of an inch.
Since thermocouple thermometers respond so rapidly, the temperature can be quickly checked in a number of locations to ensure that the food is safely cooked. This is especially useful for cooking large foods, such as roasts or turkeys, when checking the temperature in more than one place is advised. The thin probe of the thermocouple also enables it to accurately read the temperature of thin foods such as hamburger patties, pork chops, and chicken breasts.
Thermocouples are not designed to remain in the food while it's cooking. They should be used near the end of the estimated cooking time to check for final cooking temperatures. To prevent overcooking, check the temperature before the food is expected to finish cooking.
Thermocouples can be calibrated for accuracy.
For more information of food industry thermocouples, contact Duro-Sense Corporation by calling 310-533-6877 or visiting https://duro-sense.com.
Monday, March 25, 2019
A Pro and Con Comparison of Thermocouples and RTDs
Thermocouple Advantages
- Inexpensive
- Wide temperature range
- Various types, sizes and application methods
- Remote read back
- Read back electronics can be simple
- Usable in virtually any environment
- Requires cold junction compensation
- Slow response time
- Not as accurate as many other devices without good CJC and calibration
- Susceptible to noise
- Connection cable/wire is expensive compared to copper conductors
- Cable/wire length is limited
- More linear than thermocouples
- Cold junction not an issue
- Special cable/wire not needed
- Cable/wire length can be much longer than TC’s
- Better noise immunity
- More stable over time than thermocouples
- Remote read back
- Usable in virtually any environment
- More expensive than thermocouples
- More delicate than thermocouples unless encased
- Not as wide of temperature range as thermocouples
- Requires more conductors per device
- Read back electronics more complex
Tuesday, March 12, 2019
Theory of RTD Operation
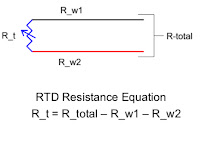
Most commonly used is the platinum 100 ohm RTD because of their stability in air and linearity. Their resistance is 100 ohms @ 0 Deg.C and increases with temperature.

Alpha is ohms per ohm per Deg.C.
The average resistance change per unit of temperature from boiling point to ice point of water:
- Rboiling – Rice point/100deg/100ohms
- 138.5 – 100.0/100/100 = .00385
Tolerance class is the amount an RTD will differ from the standard resistance curve per Deg.C.
- Class A (+/- .15 + .002*t)
- @ temp of 100DegC = +/- .35DegC
When ordering an RTD, a tolerance class will be part of the order, dependent on the application. IEC 751 stipulates that the RTD be marked with their nominal R0 value, their tolerance class, the wiring configuration and the temperature range.
![]() |
3-wire configuration |
- Pt100 / A / 3 / -100/+200 = Platinum 100 Ohm / Class A / 3-Wire / -100 to +200 Deg.C
![]() |
2-wire configuration |
Another configuration is a two wire RTD with a stand-alone loop. (Probably rarely used today).
Since the RTD is a resistance device, the resistance of the wires used to connect the RTD to the measurement meter introduces errors and must be known. This is the reason a third (or fourth), wire is used.
![]() |
3rd wire used to cancel wire error |
Then the meter reads the resistance of one of the common wires, the RTD, and the non-common wire to determine Rtotal
![]() |
Meter reading 2 common wires |

Rt = Rtotal – Rwire
Thursday, February 28, 2019
Theory of Thermocouple Operation
- A thermocouple is a simple temperature measurement device consisting of a junction of two dissimilar metals.
- Contrary to popular belief, the voltage measured (and converted to a temperature) is not a function of the junction alone. Rather it is the temperature difference (or gradient) between the junction (or hot), end and the reference (or cold), end.
- A thermocouple circuit whose junction and reference are the same temperature will measure no temperature (0V).
- If this were not true, we could create a self-sustaining voltage generator using a thermocouple, a resistive load and an oven, that would require energy only at start-up.
The temperature equation for the simplest of thermocouple circuits shown above is:
T = Tjunc – Tref
Where T is the desired measurement, Tjunc is the hot junction temperature and Tref is the reference
temperature, or cold end.
For simplicity’s sake, we use T, Tjunc and Tref here, but in reality these are voltages that are later converted to a temperature.
Cold Junctions
The temperature equation for this diagram is:
T = Tjunc – Tcj1 – Tcj2
A fundamental problem when using thermocouples is the fact the when connected to a measurement device (voltmeter or TC meter), a third metal is introduced (the connecting terminals), and two more thermocouple junctions are created. These adversely affect the temperature being measured. The new, (and unwanted), junctions are referred to as “cold junctions” and need some type of “cold junction compensation” in order to make accurate measurements.
In addition to the added variables in the previous equation, the temperature of the cold junctions
(reference end), is still not known. The following rule helps things out a bit:
- If both TC connections to the meter are of the same metal or alloy, they cancel each other and have no affect on the measurement, as long both connections are at the same temperature (which can be assumed).
Since the definition of a thermocouple states that it must be of dissimilar metals, a second thermocouple must be introduced to the circuit to achieve this. This was the first of what is commonly called “cold junction compensation”
By adding a second series thermocouple suspended in an ice bath, the cold junctions at the meter are of identical metals and cancel each other. In addition, the temperature of the ice bath is known to be 0 Deg. C and becomes the reference end of the thermocouple.
The temperature equation is now simplified and once again becomes:
The temperature equation is now simplified and once again becomes:
T = Tjunc – Tref
While the ice bath reference junction eliminates errors, it is clearly impractical for most, if not all applications. Fortunately, all of today’s thermocouple read back options (meters, chart recorders, PLCs, etc.), come equipped with cold junction compensation, usually a thermistor and associated circuitry and software. By taking the cold junction worries out of the picture, the thermocouple remains one of the simplest, most robust and widely used temperature measurement devices around.
Subscribe to:
Posts (Atom)