When two dissimilar metal wires are joined together at one end, a voltage is produced at the other end that is approximately proportional to temperature. That is to say, the junction of two different metals behaves like a temperature-sensitive battery. This form of electrical temperature sensor is called a thermocouple:
This phenomenon provides us with a simple way to electrically infer temperature: simply measure the voltage produced by the junction, and you can tell the temperature of that junction. And it would be that simple, if it were not for an unavoidable consequence of electric circuits: when we connect any kind of electrical instrument to the thermocouple wires, we inevitably produce another junction of dissimilar metals. The following schematic shows this fact, where the iron-copper junction J1 is necessarily complemented by a second iron-copper junction J2 of opposing polarity:
Junction J1 is a junction of iron and copper – two dissimilar metals – which will generate a voltage related to temperature. Note that junction J2, which is necessary for the simple fact that we must somehow connect our copper-wired voltmeter to the iron wire, is also a dissimilar-metal junction which will also generate a voltage related to temperature. Further note how the polarity of junction J2 stands opposed to the polarity of junction J1 (iron = positive ; copper = negative). A third junction (J3) also exists between wires, but it is of no consequence because it is a junction of two identical metals which does not generate a temperature-dependent voltage at all.
The presence of this second voltage-generating junction (J2) helps explain why the voltmeter registers 0 volts when the entire system is at room temperature: any voltage generated by the iron- copper junctions will be equal in magnitude and opposite in polarity, resulting in a net (series-total) voltage of zero. Only when the two junctions J1 and J2 are at different temperatures will the voltmeter register any voltage at all.
We may express this relationship mathematically as follows: Vmeter = VJ1 − VJ2
With the measurement (J1) and reference (J2) junction voltages opposed to each other, the voltmeter only “sees” the difference between these two voltages.
Thus, thermocouple systems are fundamentally differential temperature sensors. That is, they provide an electrical output proportional to the difference in temperature between two different points. For this reason, the wire junction we use to measure the temperature of interest is called the measurement junction while the other junction (which we cannot eliminate from the circuit) is called the reference junction (or the cold junction, because it is typically at a cooler temperature than the process measurement junction).
For more information on this subject, contact Duro-Sense, Inc. by visiting https://duro-sense.com or by calling 310-533-6877.
Reprinted from "Lessons In Industrial Instrumentation" by Tony R. Kuphaldt – under the terms and conditions of the Creative Commons Attribution 4.0 International Public License.
A blog providing information about industrial temperature measurement, specifically in the areas of temperature sensors. The posts will contain educational information about thermocouples, RTDs, and other common types of temperature sensors. The application of these sensors will focus on aerospace, aircraft, research and development, medical, chemical, plastics processing, and power generation industries. For more, visit Duro-Sense.com or call 310-533-6877.
Tuesday, June 26, 2018
Tuesday, June 19, 2018
Thermocouple Types, Materials of Composition, and Temperature Ranges
Nickel-Alloy Thermocouples
Type E:
(pos) 90% Nickel / 10% Chromium;
(neg) 55% Copper / 45% Nickel (Constantan)
32 to 1600°F, 0 to 870°C
Type J:
(pos) 100% Iron
(neg) 55% Copper / 45% Nickel (Constantan)
32 to 1400°F, 0 to 760°C
Type K:
(pos) 90% Nickel / 10% Chromium
(neg) 95% Nickel / 2% Aluminum / 2% Manganese / 1% Silicon
32 to 2300°F, 0 to 1260°C
Type M:
(pos) 82% Nickel / 18% Molybdenum
(neg) 99.2% Nickel / 0.8% Cobalt
-58 to 2570°F, -50 to 1410°C
Type N:
(pos) 84.5% Nickel / 14% Chromium / 1.5% Silicon
(neg) 95.4% Nickel / 4.5% Silicon / 0.1% Magnesium
32 to 2300°F, 0 to 1260°C
Type T:
(pos) 100% Copper
(neg) 55% Copper / 45% Nickel (Constantan)
-328 to 700°F, -200 to 370°C
Platinum/rhodium-Alloy thermocouples
Type B:
(pos) 70% Platinum / 30% Rhodium
(neg) 94% Platinum / 6% Rhodium
1600 to 3100°F, 871 to 1704°C
Type R:
(pos) 87% Platinum / 13% Rhodium
(neg) 100% Platinum
1000 to 2700°F, 538 to 1482°C
Type S:
(pos) 90% Platinum / 10% Rhodium
(neg) 100% Platinum
1000 to 2700°F, 538 to 1482°C
Tungsten/Rhenium-Alloy Thermocouples
Type C:
(pos) 95% Tungsten / 5% Rhenium
(neg) 74% Tungsten / 26% Rhenium
32 to 4200°F, 0 to 2315°C
Chromel–Gold/Iron-Alloy Thermocouples
Type P:
(pos) 55% Palladium / 31% Platinum / 14% Gold
(neg) 65% Gold / 35% Palladium
32 to 2543°F, 0 to 1395°C
Friday, June 8, 2018
Precision RTD's (Resistance Temperature Detectors)
Duro-Sense RTDs, thermowells, and accessories provide high quality solutions to the aerospace, aviation, process control, medical, R&D, power generation, alternative energy, plastics, primary metals, high-tech and OEM industries.
https://duro-sense.com
310-533-6877
https://duro-sense.com
310-533-6877
Friday, May 25, 2018
Power Plant Temperature Sensors
Power plants (generating facilities) transform the mechanical energy of a spinning generator into electrical energy. Heat (from flame, nuclear reaction, or chemical reaction) is used to create steam that, in turn, produces the mechanical energy to drive turbines. There are many areas where precision temperature measurement and monitoring is critical to keep power plant systems running. Thermocouples and RTD sensors provide accurate, repeatable, and reliable measurement.
Duro-Sense
https://duro-sense.com
Phone: 310-533-6877
Duro-Sense
https://duro-sense.com
Phone: 310-533-6877
Labels:
Duro-Sense,
industrial thermocouple,
power generation,
power plant,
powergen,
RTD
Wednesday, May 16, 2018
RTD and Thermocouple Selection and Location for Optimal Control
![]() |
Loop diagram * |
Most temperature control loops have (5) four major components:
1) The media to be heated (e.g. metal platen, a tank of liquid, a stream of gas)
2) A energy source (e.g. electric heater, steam, hot oil, flame)
3) A temperature sensor (thermocouple, RTD)
4) A controller (e.g. electronic thermostat, PID controller)
5) Control element (e.g. control valve, SCR, SSR)
Temperature controllers provide sophisticated functions that "learn" or understand the relationship between available power and sensor temperature. They then adjust the amount of energy (heat) added, based on the current reading of the sensor and the desired temperature setpoint. Unfortunately, temperature controllers are often relied upon to overcome the oversights and inadequacies of poor control loop design.
![]() |
Lag time * |
In the most ideal situation, temperature sensors, the energy source and process media would all be at the same physical location. Since it's virtually impossible to accomplish this, compromises have to be made to allow for the mechanical, physical, and electrical realities of the application. Here are some practical recommendations for sensor selection and placement to improve temperature loop performance:
- Thermocouples, because of their low mass generally have a response advantage over RTDs.
- Exposed junction thermocouples are the fastest responding (least lag) sensor choice, but they are also the most prone to physical and chemical damage.
- Narrow, sheathed, grounded junction magnesium oxide insulated thermocouples are nearly as fast as exposed junctions, and provide protection from the process media.
- Applications that require protection sheaths and thermowells for RTDs and thermocouples increase sensor lag time.
- An immersion length of at least 10 times the diameter of the thermowell or sensor sheath should be used to minimize heat loss along the sensor sheath or thermowell wall from tip to process connection.
- Where possible, insert the temperature sensor in a pipe elbow into the oncoming flow.
- Tapered, swaged, or stepped thermowells are faster responding
- Always make sure the fit between sensor outer diameter and thermowell inner diameter is tight, and that the tip of the sensor is in direct contact with the thermowell.
* Images courtesy of Tony Kuphaldt and his book "Lessons In Industrial Instrumentation"
Thursday, May 3, 2018
Advantages and Disadvantages of Thermocouples
![]() |
Industrial thermocouples in ceramic protection tubes (Duro-Sense) |
The thermocouple's primary disadvantage is their weak output signal and their susceptibility to electrical noise. The mV signal generated is so small it requires conditioning, namely amplification and linearization. The good news is this conditioning is built-in to and provided by the TC's corresponding controller, indicator or transmitter. Calibration drift due to oxidation, contamination, or other physical changes to the alloys is another problem associated with thermocouples, requiring a facility to implement periodic recalibration procedures. Lastly, thermocouples require alloy-matching thermocouple extension wire when running lead wires any distance from sensor to instrument. This adds cost, as thermocouple extension wire is more expensive than standard wire.
Despite these concerns, thermocouples are widely used in industry because of their relative low cost, ruggedness, wide selection of operating ranges, and versatility in size, shape, and configuration. They have been used in millions of process control applications for over a generation, and provide an excellent balance of performance, cost, and simplicity. Successful application depends on knowing thermocouple's strengths and weaknesses, and consulting with an applications expert prior to specifying or installing any temperature sensor is always recommended to ensure the sensor's longest life and best performance.
Friday, April 27, 2018
Thermocouple Junction Configurations
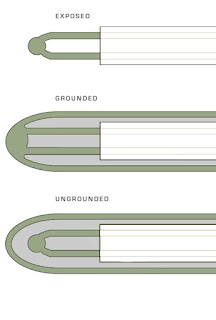
insulation, and the a welded wire sensing junction. Many thermocouple designs also include a stainless steel sheath that protects the thermocouple from vibration, shock, and corrosion.
A thermocouple has three variations of sensing tip (or junction):
- Exposed junction, where the exposed wire tips and welded bead have no covering or protection.
- Grounded junction, where the welded bead is in physical contact with the thermocouple's sheath.
- Ungrounded junction, where the tip is inside the thermocouple sheath, but is electrical (and somewhat thermally) insulated from the sheath (no sheath contact).
Grounded junction thermocouples provide fast response and are mechanically more robust, with a metallic sheath that protects the thermocouple both mechanically and from contaminants. But because their sensing tip is in contact with the external sheath, their signal still can be affected by externally induced or conducted electrical noise.
Ungrounded thermocouples, like grounded, are protected mechanically and from ambient contaminants by their sheath. However, their sensing junctions are kept separate from their metallic sheath, isolating the junction from external electrical interference. This separation does come at a small cost in temperature sensing responsiveness though.
For safety, precision, and optimum performance, always talk to an applications specialist when applying temperature sensors. A short phone call can prevent major headaches and lost time in troubleshooting a misapplied thermocouple.
Subscribe to:
Posts (Atom)