A blog providing information about industrial temperature measurement, specifically in the areas of temperature sensors. The posts will contain educational information about thermocouples, RTDs, and other common types of temperature sensors. The application of these sensors will focus on aerospace, aircraft, research and development, medical, chemical, plastics processing, and power generation industries. For more, visit Duro-Sense.com or call 310-533-6877.
Sunday, December 30, 2018
Wednesday, December 12, 2018
Happy Holidays from Duro-Sense!
From all of us at Duro-Sense, we wish our customers, partners and vendors a safe and happy holiday season and a wonderful 2019!
Monday, December 10, 2018
Duro-Sense a Critical Partner in Hydrogen Contamination Detector
We take for granted the gasoline (or diesel) we put in our cars and trucks is free from contaminants when pumped in to our gas tanks. The purity we've come to expect at the fuel pump didn't happen overnight. It took many years, and thousands of engineering hours, to develop the refining processes that produces today's clean gasoline and diesel.
Fuel Cell Vehicles are a category of electric vehicle (EV's). Fuel cell vehicles use hydrogen gas (H2) to power an electric motor. Unlike conventional vehicles which run on gasoline or diesel, fuel cell cars and trucks combine hydrogen and oxygen to produce electricity to drive the motor.
Similar to the path that gasoline and diesel processing took toward purity, the use of H2 as feedstock for fuel cells in transportation has driven requirements for H2 purity standards to very strict levels. This push has also elevated the need for cost-effective and reliable instruments that can sample H2 near the nozzle of a delivery pump, and either certify acceptability or provide a signal to shut off the fuel distribution system.
Duro-Sense Corporation, a California based manufacturer of high quality temperature sensors, is part of a team working under a DOE funded research program to develop a Hydrogen Contamination Detector. The sensor, which will be installed at hydrogen fueling stations, will detect poor quality hydrogen gas before entering the fuel cell vehicle. The sensor is intended to detect multiple impurities at extremely low levels in hydrogen to prevent fuel cell performance degradation.
Duro-Sense is designated as the industrial partner and vendor aiding in defining the commercial manufacturability of the Hydrogen Contamination Detector.
As part of their preliminary work, a thermocouple embodiment was selected as a cost-effective platform for the Hydrogen Contamination Detector because:
- Direct Commercial Availability
- Proven History of Reliability and Robustness
- Adaptability of Conductor Materials for Most
- Appropriate Catalyst for Each Contaminant
- Ability to Incorporate up to 12 Conductors a Single Thermocouple, Reducing Fluid Stream Penetrations
The Hydrogen Contamination Detector project is still in its very early stages, and research and development continues, subject to funding and continued interest in alternative fuel technology.
For more information, contact Duro-Sense at 310-533-6877 of visit their web site at https://duro-sense.com.
Tuesday, December 4, 2018
3 Bottom Line Criteria to Help You Choose Between Thermocouples and RTDs
Both RTD and thermocouple probes monitor temperature but which one is right for your application?
The first question to ask yourself is what is the temperature range you are trying to monitor?
Generally, if the temperature is above a hundred and fifty degrees Celsius, a thermocouple would be used. For anything below a hundred and fifty degrees Celsius, an RTD would be used.
The next question to ask is what is the required sensor accuracy?
RTDs provide more accurate readings with repeatable results, this is why RTDs are typically used when temperatures are within its monitoring range.
The last question is what is the purchase budget and how many do you need?
Thermocouples can be up to three times less expensive than RTD probes making thermocouples a good choice when purchasing a large quantity or when the budget is tight
These three criteria are VERY basic, and intended just to point you in the right direction. There are many other differences between thermocouples and RTDs that need to be understood before application. Always consult a temperature sensor application expert prior to installing or specifying a thermocouple or RTD where failure can cause harm.
Duro-Sense Corporation
https://duro-sense.com
The first question to ask yourself is what is the temperature range you are trying to monitor?
Generally, if the temperature is above a hundred and fifty degrees Celsius, a thermocouple would be used. For anything below a hundred and fifty degrees Celsius, an RTD would be used.
The next question to ask is what is the required sensor accuracy?
RTDs provide more accurate readings with repeatable results, this is why RTDs are typically used when temperatures are within its monitoring range.
The last question is what is the purchase budget and how many do you need?
Thermocouples can be up to three times less expensive than RTD probes making thermocouples a good choice when purchasing a large quantity or when the budget is tight
These three criteria are VERY basic, and intended just to point you in the right direction. There are many other differences between thermocouples and RTDs that need to be understood before application. Always consult a temperature sensor application expert prior to installing or specifying a thermocouple or RTD where failure can cause harm.
Duro-Sense Corporation
https://duro-sense.com
(310) 533-6877
Wednesday, November 28, 2018
Best Practice for Mounting Thermocouples in Pipes
![]() |
Diagram 1 - Not recommended. |
There are however, recommended practices for placing thermocouples in the piping flow stream.
As you can see from diagram 1, placing the thermocouple in a tee, positioned perpendicular to flow is not recommended. This is because the conduction along the sensing area may be non-negligible and could bias the measurement, depending on the liquid and ambient temperatures. In addition it may be hard to know precisely where the measurement junction is located along the cross section of the pipe in this configuration.
Ideally they should be mounted in a tee where an elbow would normally be used as you see in diagram 2. If possible the thermocouple should be oriented along the normal flow direction, and the measurement located downstream of the T-bend (the T will help mix the liquid if it is not thermally uniform).
![]() |
Diagram 2 - Recommended orientation. |
![]() |
Diagram 3 - Use U shape if there is no convenient placement for a tee. |
For more information, contact Duro-Sense by calling 310-533-6877 or visit their web site at https://duro-sense.com.
Monday, November 12, 2018
Friday, November 9, 2018
Platinum Resistance Temperature Detectors
Platinum Resistance Thermometers Detectors (RTDs) rely on the fact that platinum, like many other metals, exhibits increased electrical resistance as temperature rises. For example, a conventional RTD designed to provide 100 Ohms at 0 °C has a resistance in the neighborhood of 80 Ohms at -50 °C and 120 Ohms at 50 °C, or a sensitivity of about 0.4 Ohms per degree. RTDs constructed to particularly exacting specifications, termed Standard Platinum Resistance Thermometers, are named as the defining measurement tools for interpolating temperatures under ITS-90. In general, RTDs can have high accuracy (0.01 °C), stability, and repeatability across a wide range of temperatures from -200 °C to 500 °C.
Typically the platinum element is formed into thick or thin films, or the platinum wire is arranged in two, three or four helical coils (see diagram, right) – the more coils, the higher the sensitivity. The film or wire is placed inside a glass or ceramic enclosure, and can be supported by loose or compacted MgO. Platinum-based leads connect the probe unit to the thermometer electronics, which convert the electrical signal to temperature.
RTDs are broadly divided into two groups: Industrial RTDs and Standard Platinum Resistance Thermometers, depending on sensitivity and robustness. ASTM and IEC define several classes of RTDs, each with a different set of specifications. An ASTM "Class A" unit, for example, has an out-of-the-box tolerance — maximum permissible error — that ranges from 0.47 °C at -200 °C to 0.13 °C at 0 °C to 0.98 °C at 500 °C.
Advantages
Disadvantages
Typically the platinum element is formed into thick or thin films, or the platinum wire is arranged in two, three or four helical coils (see diagram, right) – the more coils, the higher the sensitivity. The film or wire is placed inside a glass or ceramic enclosure, and can be supported by loose or compacted MgO. Platinum-based leads connect the probe unit to the thermometer electronics, which convert the electrical signal to temperature.
RTDs are broadly divided into two groups: Industrial RTDs and Standard Platinum Resistance Thermometers, depending on sensitivity and robustness. ASTM and IEC define several classes of RTDs, each with a different set of specifications. An ASTM "Class A" unit, for example, has an out-of-the-box tolerance — maximum permissible error — that ranges from 0.47 °C at -200 °C to 0.13 °C at 0 °C to 0.98 °C at 500 °C.
Advantages
- Wide temperature range
- Resistance-temperature relationship is well characterized.
- Rugged construction in industrial RTDs
- Available in different shapes and sizes – application specific
- Can be used with a digital temperature read-out device.
Disadvantages
- Mechanical shock and vibration will cause drift.
- Deterioration at elevated temperatures (e.g., >500 °C)
- 2-and 3-wire devices need lead-wire compensation.
- Non-hermetically sealed RTDs will deteriorate in environments with excessive moisture.
Post abstracted from "Mercury Thermometer Alternatives: Platinum Resistance Thermometers (PRTs)" by NIST.
Wednesday, October 31, 2018
Thermocouple Extension Wire
In every thermocouple circuit there must be both a measurement junction and a reference junction: this is an inevitable consequence of forming a complete circuit (loop) using dissimilar-metal wires. As we already know, the voltage received by the measuring instrument from a thermocouple will be the difference between the voltages produced by the measurement and reference junctions.
Since the purpose of most temperature instruments is to accurately measure temperature at a specific location, the effects of the reference junction’s voltage must be “compensated” for by some means, either a special circuit designed to add an additional canceling voltage or by a software algorithm to digitally cancel the reference junction’s effect.
Since the purpose of most temperature instruments is to accurately measure temperature at a specific location, the effects of the reference junction’s voltage must be “compensated” for by some means, either a special circuit designed to add an additional canceling voltage or by a software algorithm to digitally cancel the reference junction’s effect.
In order for reference junction compensation to be effective, the compensation mechanism must “know” the temperature of the reference junction. This fact is so obvious, it hardly requires mentioning. However, what is not so obvious is how easily this compensation may be unintentionally defeated simply by installing a different type of wire in a thermocouple circuit.
To illustrate, let us examine a simple type K thermocouple installation, where the thermocouple connects directly to a panel-mounted temperature indicator by long wires:
Like all modern thermocouple instruments, the panel-mounted indicator contains its own internal reference junction compensation, so that it is able to compensate for the temperature of the reference junction formed at its connection terminals, where the internal (copper) wires of the indicator join to the chromel and alumel wires of the thermocouple. The indicator senses this junction temperature using a small thermistor thermally bonded to the connection terminals.
Now let us consider the same thermocouple installation with a length of copper cable (two wires) joining the field-mounted thermocouple to the panel-mounted indicator:
Even though nothing has changed in the thermocouple circuit except for the type of wires joining the thermocouple to the indicator, the reference junction has completely shifted position. What used to be a reference junction (at the indicator’s terminals) is no longer, because now we have copper wires joining to copper wires. Where there is no dissimilarity of metals, there can be no thermoelectric potential. At the thermocouple’s connection “head,” however we now have a joining of chromel and alumel wires to copper wires, thus forming a reference junction in a new location at the thermocouple head. What is worse, this new location is likely to be at a different temperature than the panel-mounted indicator, which means the indicator’s reference junction compensation will be compensating for the wrong temperature.
Now let us consider the same thermocouple installation with a length of copper cable (two wires) joining the field-mounted thermocouple to the panel-mounted indicator:
Even though nothing has changed in the thermocouple circuit except for the type of wires joining the thermocouple to the indicator, the reference junction has completely shifted position. What used to be a reference junction (at the indicator’s terminals) is no longer, because now we have copper wires joining to copper wires. Where there is no dissimilarity of metals, there can be no thermoelectric potential. At the thermocouple’s connection “head,” however we now have a joining of chromel and alumel wires to copper wires, thus forming a reference junction in a new location at the thermocouple head. What is worse, this new location is likely to be at a different temperature than the panel-mounted indicator, which means the indicator’s reference junction compensation will be compensating for the wrong temperature.
The only practical way to avoid this problem is to keep the reference junction where it belongs: at the terminals of the panel-mounted instrument where the ambient temperature is measured and the reference junction’s effects accurately compensated. If we must install “extension” wire to join a thermocouple to a remotely-located instrument, that wire must be of a type that does not form another dissimilar-metal junction at the thermocouple head, but will form one at the receiving instrument.
An obvious approach is to simply use thermocouple wire of the same type as the installed thermocouple to join the thermocouple to the indicator. For our hypothetical type K thermocouple, this means a type K cable installed between the thermocouple head and the panel-mounted indicator:
With chromel joining to chromel and alumel joining to alumel at the head, no dissimilar-metal junctions are created at the thermocouple. However, with chromel and alumel joining to copper at the indicator (again), the reference junction has been relocated to its rightful place. This means the thermocouple head’s temperature will have no effect on the performance of this measurement system, and the indicator will be able to properly compensate for any ambient temperature changes at the panel as it was designed to do. The only problem with this approach is the potential expense of thermocouple-grade cable. This is especially true with some types of thermocouples, where the metals used are somewhat exotic (e.g. types R, S, and B).
A more economical alternative, however, is to use something called extension-grade wire to make the connection between the thermocouple and the receiving instrument. “Extension-grade” thermocouple wire is made less expensive than full “thermocouple-grade” wire by choosing metal alloys similar in thermo-electrical characteristics to the real thermocouple wires within modest temperature ranges. So long as the temperatures at the thermocouple head and receiving instrument terminals don’t get too hot or too cold, the extension wire metals joining to the thermocouple wires and joining to the instrument’s copper wires need not be precisely identical to the true thermocouple wire alloys. This allows for a wider selection of metal types, some of which are substantially less expensive than the measurement-grade thermocouple alloys. Also, extension-grade wire may use insulation with a narrower temperature rating than thermocouple-grade wire, reducing cost even further.
Extension-grade cable is denoted by a letter “X” following the thermocouple letter. For our hypothetical type K thermocouple system, this would mean type “KX” extension cable:
Thermocouple extension cable also differs from thermocouple-grade (measurement) cable in the coloring of its outer jacket. Whereas thermocouple-grade cable is typically brown in exterior color, extension-grade cable is usually colored to match the thermocouple plug (yellow for type K, black for type J, blue for type T, etc.)
For more information on thermocouple extension wire, contact Duro-Sense by visiting https://duro-sense.com or by calling 310-533-6877
For more information on thermocouple extension wire, contact Duro-Sense by visiting https://duro-sense.com or by calling 310-533-6877
Reprinted from "Lessons In Industrial Instrumentation" by Tony R. Kuphaldt – under the terms and conditions of the Creative Commons Attribution 4.0 International Public License.
Wednesday, October 24, 2018
The MgO Thermocouple
![]() |
Magnesium oxide |
While magnesium oxide is the favored high temperature insulating material, many others have been tested. Some examples are aluminum oxide, crystalline silica, and beryllium oxide. For various reasons, ranging from cost, inferior mechanical, poor electrical, and safety issues, magnesium oxide outperforms other powders in industrial applications.
![]() |
MgO cable cutaway |
![]() |
MgO thermocouple |
MgO thermocouples are known for high dielectric strength, durability, malleability and quick response to temperature fluctuations. They can be used for process applications up to 2400°F and, because the measuring junction can also be sealed from the environment, they are recommended for use in high pressure, high moisture, corrosive, and environments.
For more information on MgO thermocouples, contact Duro-Sense Corporation at https://duro-sense.com or by calling 310-533-6877
Wednesday, October 10, 2018
Overview of Thermocouple Types and Ranges
Thermocouples have been classified by the International Society of Automation (formerly Instrument Society of America) and the American National Standards Institute (ANSI), and are available for temperatures ranging from -200 deg. to 1700 deg.C (-330 deg. to 3100 deg.F). These standard tolerance thermocouples range in tolerance from ±0.5 percent to ±2 percent of true temperature. The table below presents commonly available thermocouple types and operating ranges.
Thermocouples must be selected to meet the conditions of the application. Thermocouple and extension wires (used to transmit the voltage from the thermocouple to the monitoring point) are generally specified and ordered by their ANSI letter designations for wire types. Positive and negative legs are identified by the letter suffixes P and N, respectively. General size and type recommendations are based on length of service, temperature, type of atmosphere (gas or liquid constituents), and desired response times. Smaller wire gauges provide faster response but do not last as long under adverse conditions. Conversely, larger gauges provide longer service life but with longer response times. Thermowells and sheaths are recommended by thermocouple manufacturers for the extension of thermocouple life. Instruments used to convert thermocouple voltage to temperature scales are coded using the same letter designations. Failure to use matching thermocouples and instruments will result in erroneous readings.
Type J thermocouples use iron for the positive leg and copper-nickel (constantin) alloys for the negative leg. They may be used unprotected where there is an oxygen-deficient atmosphere, but a thermowell is recommended for cleanliness and generally longer life. Because the iron (positive leg) wire oxidizes rapidly at temperatures over 1000 deg.F, manufacturers recommend using larger gauge wires to extend the life of the thermocouple when temperatures approach the maximum operating temperature.
Type K thermocouples use chromium-nickel alloys for the positive leg and copper alloys for the negative leg. They are reliable and relatively accurate over a wide temperature range. It is a good practice to protect Type K thermocouples with a suitable ceramic tube, especially in reducing atmospheres. In oxidizing atmospheres, such as electric arc furnaces, tube protection may not be necessary as long as other conditions are suitable; however, manufacturers still recommend protection for cleanliness and prevention of mechanical damage. Type K thermocouples generally outlast Type J, because the iron wire in a Type J thermocouple oxidizes rapidly at higher temperatures.
Type N thermocouples use nickel alloys for both the positive and negative legs to achieve operation at higher temperatures, especially where sulfur compounds are present. They provide better resistance to oxidation, leading to longer service life overall.
Type T thermocouples use copper for the positive leg and copper-nickel alloys for the negative leg. They can be used in either oxidizing or reducing atmospheres, but, again, manufacturers recommend the use of thermowells. These are good stable thermocouples for lower temperatures.
Types S, R, and B thermocouples use noble metals for the leg wires and are able to perform at higher temperatures than the common Types J and K. They are, however, easily contaminated, and reducing atmospheres are particularly detrimental to their accuracy. Manufacturers of such thermocouples recommend gas-tight ceramic tubes, secondary porcelain protective tubes, and a silicon carbide or metal outer protective tube depending on service locations.
For more information about thermocouples, contact Duro-Sense Corporation by visiting https://duro-sense.com or calling 310-533-6877.
![]() |
Commonly Available Thermocouple Types and Operating Ranges |

Type K thermocouples use chromium-nickel alloys for the positive leg and copper alloys for the negative leg. They are reliable and relatively accurate over a wide temperature range. It is a good practice to protect Type K thermocouples with a suitable ceramic tube, especially in reducing atmospheres. In oxidizing atmospheres, such as electric arc furnaces, tube protection may not be necessary as long as other conditions are suitable; however, manufacturers still recommend protection for cleanliness and prevention of mechanical damage. Type K thermocouples generally outlast Type J, because the iron wire in a Type J thermocouple oxidizes rapidly at higher temperatures.
Type N thermocouples use nickel alloys for both the positive and negative legs to achieve operation at higher temperatures, especially where sulfur compounds are present. They provide better resistance to oxidation, leading to longer service life overall.
Type T thermocouples use copper for the positive leg and copper-nickel alloys for the negative leg. They can be used in either oxidizing or reducing atmospheres, but, again, manufacturers recommend the use of thermowells. These are good stable thermocouples for lower temperatures.
Types S, R, and B thermocouples use noble metals for the leg wires and are able to perform at higher temperatures than the common Types J and K. They are, however, easily contaminated, and reducing atmospheres are particularly detrimental to their accuracy. Manufacturers of such thermocouples recommend gas-tight ceramic tubes, secondary porcelain protective tubes, and a silicon carbide or metal outer protective tube depending on service locations.
For more information about thermocouples, contact Duro-Sense Corporation by visiting https://duro-sense.com or calling 310-533-6877.
Friday, September 28, 2018
Advantage and Disadvantages of Common Temperature Sensors
THERMOCOUPLE
![]() |
Thermocouple |
Thermocouple Advantages:
- Self-powered
- Simple
- Rugged
- Inexpensive
- Many applications
- Wide temperature range
- Fast response
- Nonlinear output signal
- Low voltage
- Reference required
- Accuracy is function of two separate measurements
- Least sensitive
- Sensor cannot be recalibrated
- Least stable
RTD
![]() |
RTD |
RTD Advantages:
- More stable at moderate temperatures
- High levels of accuracy
- Relatively linear output signal
- Expensive
- Self-heating
- Lower temperature range
THERMISTOR
![]() |
Thermistor |
Thermistor Advantages:
- High output
- Fast
- Two-wire ohms measurement
- Nonlinear
- Limited temperature range
- Fragile
- Current source required
- Self-heating
Sunday, September 23, 2018
Monday, September 10, 2018
Thermowells
![]() |
Thermowell (Duro-Sense) |
Thermowells may be made out of any material that is thermally conductive, pressure-tight, and not chemically reactive with the process. Most thermowells are formed out of either metal (stainless steel or other alloy) or ceramic materials. A simple diagram showing a thermowell in use with a temperature sensor (RTD) is shown here:
As useful as thermowells are, they are not without their caveats. All thermowells, no matter how well they may be installed, increase the first-order time lag of the temperature sensor by virtue of their mass and specific heat value. It should be intuitively obvious that a few pounds of metal will not heat up and cool down as fast as a few ounces’ worth of RTD or thermocouple, and therefore the addition of a thermowell to the sensing element will decrease the responsiveness of any temperature- sensing element. What is not so obvious is that such time lags, if severe enough, may compromise the stability of feedback control. A control system receiving a “delayed” temperature measurement will not see the live temperature of the process in real time due to this lag.
![]() |
RTD with Thermowell |
Reprinted from Lessons In Industrial Instrumentation by Tony R. Kuphaldt – under the terms and conditions of the Creative Commons Attribution 4.0 International Public License.
Tuesday, August 28, 2018
Temperature Transmitters
![]() |
Temperature Transmitters (Duro-Sense) |
Analog Transmitters: These transmitters are designed on analog circuit technology. They normally offer basic functions such as temperature linearization and sensor break technology. Sometimes they are adjustable for different measuring ranges, often with a fast response time.
Digital Transmitters: This transmitter type is mainly based on a microprocessor. They are often called intelligent transmitters, because they normally offer many extra features, which are not possible to realize in analog transmitters.
In-Head Transmitters: These transmitters are designed for mounting in the connection heads of temperature sensors. All Duro-Sense in-head transmitters fit into DIN B heads or larger. Special care has to be devoted to the ruggedness because of the harsh conditions that sometimes exist.
DIN Rail Transmitters: DIN rail transmitters are designed to be snapped onto a DIN rail. Duro-Sense DIN rail transmitters fit on a 35mm rail according to DIN EN 50022.
RTD Transmitters: RTD transmitters are used only for RTD sensors. (Pt100, Pt1000, Ni100, etc.). Normally they can handle only one RTD type. Most Duro-Sense transmitters can handle more than one type of RTD and are either fix- ranged or adjustable. They all have linear output.

Analog Output: The output signal is a current (4-20mA). Some transmitters are available with 0-20mA or 0-10mA output. The signal is normally proportional to the measured value within a defined measurement range.
Digital Output: The measured value (temperature) is presented as a binary coded message. So called Fieldbus transmitters use this technique. The Fieldbus transmitters on the market today use different standards for the communication thus creating some problems when integrating them with other instrumentation. Examples of standard available are: PROFIBUS, Interbus, Foundation Fieldbus, LonWorks and CAN-bus.
Analog and Digital Output: The HART transmitters have an analog output with a superimposed digital signal on the same wires. Typically, the analog signal is used for normal measurements and the digital signal only for temporary measurements, because of the low communication speed. The digital signal is mainly used for configuration and status information.
Isolated Transmitters: Isolated transmitters have no leading connections between circuits that are isolated from each other. The isolation effectively eliminates the risk for circulating currents and facilitates the connection of transmitters to control systems with grounded inputs.
Non-Isolated Transmitters: These transmitters have leading connections between, for instance, input and output circuits. They should be used with care.
For more information on temperature transmitters, visit https://duro-sense.com or call 310-533-6877.
Friday, August 17, 2018
Temperature Sensors for the Toughest Applications
![]() |
Click for larger view. |
All Duro-Sense customers benefit from years of tackling difficult applications. By implementing stringent quality practices and advanced manufacturing processes, Duro-Sense continues to solve the most challenging temperature sensing applications.
Duro-Sense is a one-stop, full service provider of anything related to temperature sensing. Service. Quality. On-time delivery.
Rely on the Duro-Sense difference.
www.duro-sense.com | 310-533-6877.
Friday, August 3, 2018
Video: Comparison of Thermocouples and RTDs
The video below describes the basic differences between industrial thermocouples and RTDs.
Duro-Sense Corporation provides the thermocouples, RTDs, thermowells, and accessories to the aerospace, aviation, process control, medical, R&D, power generation, alternative energy, plastics, primary metals, high-tech and OEM industries.
https://duro-sense.com
310-533-6877
Duro-Sense Corporation provides the thermocouples, RTDs, thermowells, and accessories to the aerospace, aviation, process control, medical, R&D, power generation, alternative energy, plastics, primary metals, high-tech and OEM industries.
https://duro-sense.com
310-533-6877
Wednesday, July 18, 2018
Reliable, Robust, and Affordable Process Heating Sensors and Controls
The ability to effectively measure, monitor, and control process heating operations is essential to minimize product variability and maintain product quality. This level of control requires reliable and affordable sensors and control systems that can withstand harsh environments and not require recalibration for at least one year. Process heating could become far more effective with access to more reliable, robust, and affordable sensors and process controls. There is a need for reliable, cost effective sensors for harsh environments and for the real-time measurement of the chemical composition of the fuel, oxidant, and flue gas in combustion processes. Real-time combustion controls for multiple fuel applications could help maximize fuel flexibility, while improved sensors as part of smart control systems could increase efficiency, safety, and reliability. In electromagnetic processes, low cost, robust, and reliable sensors are needed to measure field strength, as well as sensors that can measure process parameters but are immune to direct excitation by the electromagnetic energy.
Technology opportunities for sensors and process controls to improve the overall control and
performance of process heating systems include the following:
Sensors for Harsh, High-Temperature Environments: Technologies and methods are needed to reliably monitor and control critical product parameters (temperature, chemistry, pressure, etc.), especially robust sensors to measure critical parameters in harsh combustion environments. This includes direct process measurement sensors, and more accurate and reliable thermocouples and other sensors. The development of sensors that can provide accurate readings in high-temperature environments could enable opportunities to optimize heat transfer and containment systems in those conditions.
Furnace Control: In fuel-fired equipment, reliable sensing and control technologies can provide better fuel utilization, energy savings, temperature control, and system performance over time. This includes sensors that can accurately measure compositional characteristics of fuels and oxidant; low-cost, highly reliable flame monitoring systems to control flame quality and stability; and continuous flue gas analysis. By regulating and stabilizing internal furnace pressure, pressure controllers can eliminate cold air infiltration, maintain uniform temperatures, and reduce wear that would require more frequent and costly maintenance.
Advanced Control Strategies to Optimize Process Heating: Cost-effective smart process controls that can be integrated with the overall manufacturing system are needed. Analysis of flue gases can be used to optimize the inlet fuel/air ratio. By using sensors to measure oxygen and carbon monoxide in the flue gas stream, conditions can be created for ideal combustion scenarios.

performance of process heating systems include the following:
Sensors for Harsh, High-Temperature Environments: Technologies and methods are needed to reliably monitor and control critical product parameters (temperature, chemistry, pressure, etc.), especially robust sensors to measure critical parameters in harsh combustion environments. This includes direct process measurement sensors, and more accurate and reliable thermocouples and other sensors. The development of sensors that can provide accurate readings in high-temperature environments could enable opportunities to optimize heat transfer and containment systems in those conditions.
Furnace Control: In fuel-fired equipment, reliable sensing and control technologies can provide better fuel utilization, energy savings, temperature control, and system performance over time. This includes sensors that can accurately measure compositional characteristics of fuels and oxidant; low-cost, highly reliable flame monitoring systems to control flame quality and stability; and continuous flue gas analysis. By regulating and stabilizing internal furnace pressure, pressure controllers can eliminate cold air infiltration, maintain uniform temperatures, and reduce wear that would require more frequent and costly maintenance.
Advanced Control Strategies to Optimize Process Heating: Cost-effective smart process controls that can be integrated with the overall manufacturing system are needed. Analysis of flue gases can be used to optimize the inlet fuel/air ratio. By using sensors to measure oxygen and carbon monoxide in the flue gas stream, conditions can be created for ideal combustion scenarios.
Friday, July 6, 2018
Common Terminology Used in Temperature Measurement and Process Control
Accuracy: The closeness of an indicator or reading of a measurement device to the actual value of the quantity being measured; usually expressed as ± percent of the full scale output or reading.
Drift: The change in output or set point value over long periods of time due to such factors as temperature, voltage, and time.
Hysteresis: The difference in output after a full cycle in which the input value approaches the reference point (conditions) with increasing, then decreasing values or vice versa; it is measured by decreasing the input to one extreme (minimum or maximum value), then to the other extreme, then returning the input to the reference (starting) value.
Linearity: How closely the output of a sensor approximates a straight line when the applied input is linear.
Noise: An unwanted electrical interference on signal wires.
Nonlinearity: The difference between the actual deflection curve of a unit and a straight line drawn between the upper and lower range terminal values of the deflection, expressed as a percentage of full range deflection.
Precision: The degree of agreement between a number of independent observations of the same physical quantity obtained under the same conditions.
Repeatability: The ability of a sensor to reproduce output readings when the same input value is applied to it consecutively under the same conditions.
Resolution: The smallest detectable increment of measurement.
RTD: Abbreviation for "resistance temperature detector". Resistance temperature detectors are temperature sensors that are widely used because of their high accuracy, stability, and linearity. They work on the principle that the resistivity of metals is dependent upon temperature; as temperature increases, resistance increases. Resistance Temperature Detector’s can withstand temperatures up to approximately 800 C (~1500 F).
Sensitivity: The minimum change in input signal to which an instrument can respond. Stability: The ability of an instrument to provide consistent output over an extended
period during which a constant input is applied.
Thermocouple: A temperature sensing device widely used because they are relatively low cost, self-powered, durable and capable sensing high temperatures. Thermocouples generate and micro voltage in relation to temperature change.
Zero balance: The ability of the transducer to output a value of zero at the electronic null
point.
Drift: The change in output or set point value over long periods of time due to such factors as temperature, voltage, and time.
Hysteresis: The difference in output after a full cycle in which the input value approaches the reference point (conditions) with increasing, then decreasing values or vice versa; it is measured by decreasing the input to one extreme (minimum or maximum value), then to the other extreme, then returning the input to the reference (starting) value.
Linearity: How closely the output of a sensor approximates a straight line when the applied input is linear.
Noise: An unwanted electrical interference on signal wires.
Nonlinearity: The difference between the actual deflection curve of a unit and a straight line drawn between the upper and lower range terminal values of the deflection, expressed as a percentage of full range deflection.
Precision: The degree of agreement between a number of independent observations of the same physical quantity obtained under the same conditions.
Repeatability: The ability of a sensor to reproduce output readings when the same input value is applied to it consecutively under the same conditions.
Resolution: The smallest detectable increment of measurement.
RTD: Abbreviation for "resistance temperature detector". Resistance temperature detectors are temperature sensors that are widely used because of their high accuracy, stability, and linearity. They work on the principle that the resistivity of metals is dependent upon temperature; as temperature increases, resistance increases. Resistance Temperature Detector’s can withstand temperatures up to approximately 800 C (~1500 F).
Sensitivity: The minimum change in input signal to which an instrument can respond. Stability: The ability of an instrument to provide consistent output over an extended
period during which a constant input is applied.
Thermocouple: A temperature sensing device widely used because they are relatively low cost, self-powered, durable and capable sensing high temperatures. Thermocouples generate and micro voltage in relation to temperature change.
Zero balance: The ability of the transducer to output a value of zero at the electronic null
point.
Monday, July 2, 2018
Tuesday, June 26, 2018
Understanding Dissimilar Metal Junctions and the Need for Reference Junctions
When two dissimilar metal wires are joined together at one end, a voltage is produced at the other end that is approximately proportional to temperature. That is to say, the junction of two different metals behaves like a temperature-sensitive battery. This form of electrical temperature sensor is called a thermocouple:
This phenomenon provides us with a simple way to electrically infer temperature: simply measure the voltage produced by the junction, and you can tell the temperature of that junction. And it would be that simple, if it were not for an unavoidable consequence of electric circuits: when we connect any kind of electrical instrument to the thermocouple wires, we inevitably produce another junction of dissimilar metals. The following schematic shows this fact, where the iron-copper junction J1 is necessarily complemented by a second iron-copper junction J2 of opposing polarity:
Junction J1 is a junction of iron and copper – two dissimilar metals – which will generate a voltage related to temperature. Note that junction J2, which is necessary for the simple fact that we must somehow connect our copper-wired voltmeter to the iron wire, is also a dissimilar-metal junction which will also generate a voltage related to temperature. Further note how the polarity of junction J2 stands opposed to the polarity of junction J1 (iron = positive ; copper = negative). A third junction (J3) also exists between wires, but it is of no consequence because it is a junction of two identical metals which does not generate a temperature-dependent voltage at all.
The presence of this second voltage-generating junction (J2) helps explain why the voltmeter registers 0 volts when the entire system is at room temperature: any voltage generated by the iron- copper junctions will be equal in magnitude and opposite in polarity, resulting in a net (series-total) voltage of zero. Only when the two junctions J1 and J2 are at different temperatures will the voltmeter register any voltage at all.
We may express this relationship mathematically as follows: Vmeter = VJ1 − VJ2
With the measurement (J1) and reference (J2) junction voltages opposed to each other, the voltmeter only “sees” the difference between these two voltages.
Thus, thermocouple systems are fundamentally differential temperature sensors. That is, they provide an electrical output proportional to the difference in temperature between two different points. For this reason, the wire junction we use to measure the temperature of interest is called the measurement junction while the other junction (which we cannot eliminate from the circuit) is called the reference junction (or the cold junction, because it is typically at a cooler temperature than the process measurement junction).
For more information on this subject, contact Duro-Sense, Inc. by visiting https://duro-sense.com or by calling 310-533-6877.
Reprinted from "Lessons In Industrial Instrumentation" by Tony R. Kuphaldt – under the terms and conditions of the Creative Commons Attribution 4.0 International Public License.
This phenomenon provides us with a simple way to electrically infer temperature: simply measure the voltage produced by the junction, and you can tell the temperature of that junction. And it would be that simple, if it were not for an unavoidable consequence of electric circuits: when we connect any kind of electrical instrument to the thermocouple wires, we inevitably produce another junction of dissimilar metals. The following schematic shows this fact, where the iron-copper junction J1 is necessarily complemented by a second iron-copper junction J2 of opposing polarity:
Junction J1 is a junction of iron and copper – two dissimilar metals – which will generate a voltage related to temperature. Note that junction J2, which is necessary for the simple fact that we must somehow connect our copper-wired voltmeter to the iron wire, is also a dissimilar-metal junction which will also generate a voltage related to temperature. Further note how the polarity of junction J2 stands opposed to the polarity of junction J1 (iron = positive ; copper = negative). A third junction (J3) also exists between wires, but it is of no consequence because it is a junction of two identical metals which does not generate a temperature-dependent voltage at all.
The presence of this second voltage-generating junction (J2) helps explain why the voltmeter registers 0 volts when the entire system is at room temperature: any voltage generated by the iron- copper junctions will be equal in magnitude and opposite in polarity, resulting in a net (series-total) voltage of zero. Only when the two junctions J1 and J2 are at different temperatures will the voltmeter register any voltage at all.
We may express this relationship mathematically as follows: Vmeter = VJ1 − VJ2
With the measurement (J1) and reference (J2) junction voltages opposed to each other, the voltmeter only “sees” the difference between these two voltages.
Thus, thermocouple systems are fundamentally differential temperature sensors. That is, they provide an electrical output proportional to the difference in temperature between two different points. For this reason, the wire junction we use to measure the temperature of interest is called the measurement junction while the other junction (which we cannot eliminate from the circuit) is called the reference junction (or the cold junction, because it is typically at a cooler temperature than the process measurement junction).
For more information on this subject, contact Duro-Sense, Inc. by visiting https://duro-sense.com or by calling 310-533-6877.
Reprinted from "Lessons In Industrial Instrumentation" by Tony R. Kuphaldt – under the terms and conditions of the Creative Commons Attribution 4.0 International Public License.
Tuesday, June 19, 2018
Thermocouple Types, Materials of Composition, and Temperature Ranges
Nickel-Alloy Thermocouples
Type E:
(pos) 90% Nickel / 10% Chromium;
(neg) 55% Copper / 45% Nickel (Constantan)
32 to 1600°F, 0 to 870°C
Type J:
(pos) 100% Iron
(neg) 55% Copper / 45% Nickel (Constantan)
32 to 1400°F, 0 to 760°C
Type K:
(pos) 90% Nickel / 10% Chromium
(neg) 95% Nickel / 2% Aluminum / 2% Manganese / 1% Silicon
32 to 2300°F, 0 to 1260°C
Type M:
(pos) 82% Nickel / 18% Molybdenum
(neg) 99.2% Nickel / 0.8% Cobalt
-58 to 2570°F, -50 to 1410°C
Type N:
(pos) 84.5% Nickel / 14% Chromium / 1.5% Silicon
(neg) 95.4% Nickel / 4.5% Silicon / 0.1% Magnesium
32 to 2300°F, 0 to 1260°C
Type T:
(pos) 100% Copper
(neg) 55% Copper / 45% Nickel (Constantan)
-328 to 700°F, -200 to 370°C
Platinum/rhodium-Alloy thermocouples
Type B:
(pos) 70% Platinum / 30% Rhodium
(neg) 94% Platinum / 6% Rhodium
1600 to 3100°F, 871 to 1704°C
Type R:
(pos) 87% Platinum / 13% Rhodium
(neg) 100% Platinum
1000 to 2700°F, 538 to 1482°C
Type S:
(pos) 90% Platinum / 10% Rhodium
(neg) 100% Platinum
1000 to 2700°F, 538 to 1482°C
Tungsten/Rhenium-Alloy Thermocouples
Type C:
(pos) 95% Tungsten / 5% Rhenium
(neg) 74% Tungsten / 26% Rhenium
32 to 4200°F, 0 to 2315°C
Chromel–Gold/Iron-Alloy Thermocouples
Type P:
(pos) 55% Palladium / 31% Platinum / 14% Gold
(neg) 65% Gold / 35% Palladium
32 to 2543°F, 0 to 1395°C
Friday, June 8, 2018
Precision RTD's (Resistance Temperature Detectors)
Duro-Sense RTDs, thermowells, and accessories provide high quality solutions to the aerospace, aviation, process control, medical, R&D, power generation, alternative energy, plastics, primary metals, high-tech and OEM industries.
https://duro-sense.com
310-533-6877
https://duro-sense.com
310-533-6877
Friday, May 25, 2018
Power Plant Temperature Sensors
Power plants (generating facilities) transform the mechanical energy of a spinning generator into electrical energy. Heat (from flame, nuclear reaction, or chemical reaction) is used to create steam that, in turn, produces the mechanical energy to drive turbines. There are many areas where precision temperature measurement and monitoring is critical to keep power plant systems running. Thermocouples and RTD sensors provide accurate, repeatable, and reliable measurement.
Duro-Sense
https://duro-sense.com
Phone: 310-533-6877
Duro-Sense
https://duro-sense.com
Phone: 310-533-6877
Labels:
Duro-Sense,
industrial thermocouple,
power generation,
power plant,
powergen,
RTD
Wednesday, May 16, 2018
RTD and Thermocouple Selection and Location for Optimal Control
![]() |
Loop diagram * |
Most temperature control loops have (5) four major components:
1) The media to be heated (e.g. metal platen, a tank of liquid, a stream of gas)
2) A energy source (e.g. electric heater, steam, hot oil, flame)
3) A temperature sensor (thermocouple, RTD)
4) A controller (e.g. electronic thermostat, PID controller)
5) Control element (e.g. control valve, SCR, SSR)
Temperature controllers provide sophisticated functions that "learn" or understand the relationship between available power and sensor temperature. They then adjust the amount of energy (heat) added, based on the current reading of the sensor and the desired temperature setpoint. Unfortunately, temperature controllers are often relied upon to overcome the oversights and inadequacies of poor control loop design.
![]() |
Lag time * |
In the most ideal situation, temperature sensors, the energy source and process media would all be at the same physical location. Since it's virtually impossible to accomplish this, compromises have to be made to allow for the mechanical, physical, and electrical realities of the application. Here are some practical recommendations for sensor selection and placement to improve temperature loop performance:
- Thermocouples, because of their low mass generally have a response advantage over RTDs.
- Exposed junction thermocouples are the fastest responding (least lag) sensor choice, but they are also the most prone to physical and chemical damage.
- Narrow, sheathed, grounded junction magnesium oxide insulated thermocouples are nearly as fast as exposed junctions, and provide protection from the process media.
- Applications that require protection sheaths and thermowells for RTDs and thermocouples increase sensor lag time.
- An immersion length of at least 10 times the diameter of the thermowell or sensor sheath should be used to minimize heat loss along the sensor sheath or thermowell wall from tip to process connection.
- Where possible, insert the temperature sensor in a pipe elbow into the oncoming flow.
- Tapered, swaged, or stepped thermowells are faster responding
- Always make sure the fit between sensor outer diameter and thermowell inner diameter is tight, and that the tip of the sensor is in direct contact with the thermowell.
* Images courtesy of Tony Kuphaldt and his book "Lessons In Industrial Instrumentation"
Thursday, May 3, 2018
Advantages and Disadvantages of Thermocouples
![]() |
Industrial thermocouples in ceramic protection tubes (Duro-Sense) |
The thermocouple's primary disadvantage is their weak output signal and their susceptibility to electrical noise. The mV signal generated is so small it requires conditioning, namely amplification and linearization. The good news is this conditioning is built-in to and provided by the TC's corresponding controller, indicator or transmitter. Calibration drift due to oxidation, contamination, or other physical changes to the alloys is another problem associated with thermocouples, requiring a facility to implement periodic recalibration procedures. Lastly, thermocouples require alloy-matching thermocouple extension wire when running lead wires any distance from sensor to instrument. This adds cost, as thermocouple extension wire is more expensive than standard wire.
Despite these concerns, thermocouples are widely used in industry because of their relative low cost, ruggedness, wide selection of operating ranges, and versatility in size, shape, and configuration. They have been used in millions of process control applications for over a generation, and provide an excellent balance of performance, cost, and simplicity. Successful application depends on knowing thermocouple's strengths and weaknesses, and consulting with an applications expert prior to specifying or installing any temperature sensor is always recommended to ensure the sensor's longest life and best performance.
Friday, April 27, 2018
Thermocouple Junction Configurations
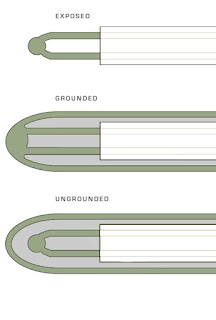
insulation, and the a welded wire sensing junction. Many thermocouple designs also include a stainless steel sheath that protects the thermocouple from vibration, shock, and corrosion.
A thermocouple has three variations of sensing tip (or junction):
- Exposed junction, where the exposed wire tips and welded bead have no covering or protection.
- Grounded junction, where the welded bead is in physical contact with the thermocouple's sheath.
- Ungrounded junction, where the tip is inside the thermocouple sheath, but is electrical (and somewhat thermally) insulated from the sheath (no sheath contact).
Grounded junction thermocouples provide fast response and are mechanically more robust, with a metallic sheath that protects the thermocouple both mechanically and from contaminants. But because their sensing tip is in contact with the external sheath, their signal still can be affected by externally induced or conducted electrical noise.
Ungrounded thermocouples, like grounded, are protected mechanically and from ambient contaminants by their sheath. However, their sensing junctions are kept separate from their metallic sheath, isolating the junction from external electrical interference. This separation does come at a small cost in temperature sensing responsiveness though.
For safety, precision, and optimum performance, always talk to an applications specialist when applying temperature sensors. A short phone call can prevent major headaches and lost time in troubleshooting a misapplied thermocouple.
Saturday, April 14, 2018
Thermocouples and RTDs Used in Power Plants
The majority of temperature measuring in a electrical generating plant are done with RTDs (resistance temperature detectors) and thermocouples (T/Cs).
RTD's are devices that produce a measurable resistance change with temperature change, while thermocouples produce a mV signal change in response to temperature change.
RTD's are constructed of a a thin conductor (nickel, platinum, copper) wrapped around a glass or ceramic bobbin, inserted into a protective sheath, and backfilled with an electrically inert, but thermally conductive, material.
Power plants historically use 100-ohm platinum, 100-ohm nickel, 120-ohm nickel, and 10-ohm copper RTDs. While providing excellent accuracy and long term stability, RTDs are prone to mechanical shock and vibration found in a generating facility. They are more expensive than thermocouples and application temperatures are generally limited to around up to 1110°F. One very attractive feature for RTDs are their inherent electrical noise immunity, a significant advantage over thermocouples. Finally, common, inexpensive instrument wire is used for connecting the RTD to the measuring instrumentation.
A thermocouple consists of two wires, made of dissimilar alloys, joined together at each end. One junction is designated the hot junction, the other junction is designated as the cold (or reference junction). When the hot junction experiences a change in temperature, a voltage is generated that is proportional to the difference in temperature between the hot and cold junctions.
T/Cs are be made of different combinations of alloys and "calibrations" for use at various temperature ranges. The most common thermocouples for the power generation industry applications under 1800 °F are type are J, K and N ; for applications over 1800 °F, types R and S are common. Aside from the obvious higher temperature capability, thermocouples provide faster response and greater shock and vibration endurance. However, thermocouples, due to the minuter signals the produce, are more susceptible to conducted and radiated electrical noise. Another concern with thermocouples are their degradation over time when used at elevated temperatures and are therefore less stable than RTDs. One final issue is the need to run costly thermocouple extension wire of the same type as the thermocouple between sensor and measuring instrument.
When in doubt about which sensor is best to apply in a power plant application, contact an application expert who will help you choose the ideal sensor for your requirements.
https://duro-sense.com
Ph: 310-533-6877
RTD's are devices that produce a measurable resistance change with temperature change, while thermocouples produce a mV signal change in response to temperature change.
RTD's are constructed of a a thin conductor (nickel, platinum, copper) wrapped around a glass or ceramic bobbin, inserted into a protective sheath, and backfilled with an electrically inert, but thermally conductive, material.
Power plants historically use 100-ohm platinum, 100-ohm nickel, 120-ohm nickel, and 10-ohm copper RTDs. While providing excellent accuracy and long term stability, RTDs are prone to mechanical shock and vibration found in a generating facility. They are more expensive than thermocouples and application temperatures are generally limited to around up to 1110°F. One very attractive feature for RTDs are their inherent electrical noise immunity, a significant advantage over thermocouples. Finally, common, inexpensive instrument wire is used for connecting the RTD to the measuring instrumentation.
A thermocouple consists of two wires, made of dissimilar alloys, joined together at each end. One junction is designated the hot junction, the other junction is designated as the cold (or reference junction). When the hot junction experiences a change in temperature, a voltage is generated that is proportional to the difference in temperature between the hot and cold junctions.
T/Cs are be made of different combinations of alloys and "calibrations" for use at various temperature ranges. The most common thermocouples for the power generation industry applications under 1800 °F are type are J, K and N ; for applications over 1800 °F, types R and S are common. Aside from the obvious higher temperature capability, thermocouples provide faster response and greater shock and vibration endurance. However, thermocouples, due to the minuter signals the produce, are more susceptible to conducted and radiated electrical noise. Another concern with thermocouples are their degradation over time when used at elevated temperatures and are therefore less stable than RTDs. One final issue is the need to run costly thermocouple extension wire of the same type as the thermocouple between sensor and measuring instrument.
When in doubt about which sensor is best to apply in a power plant application, contact an application expert who will help you choose the ideal sensor for your requirements.
https://duro-sense.com
Ph: 310-533-6877
Labels:
coal plant,
electricity,
power generation,
power plant,
powergen,
RTD,
thermocouple
Tuesday, April 3, 2018
What are Plastics Thermocouples?
![]() |
Right Angle, Bayonet Style, Plastics Thermocouples |
In most cases, plastics thermocouples are ANSI type J or type K calibration. Type J or K lead wire is available in a variety of insulation materials and protection options, such as high temperature fiberglass, PVC, stainless steel braided fiberglass, or stainless steel flexible armor cable. Electrical connections are most commonly bare leads, male thermocouple jacks, female thermocouple plugs, or spade lugs.
Bayonet designs are straight or right angle, and use industry standard bayonet fittings that easily retrofit most injection molding and plastics processing equipment. These fittings allow for adjustable depth and are spring loaded for maintaining goos contact with the media. Washer and shim style thermocouples weld or crimp the thermocouple sensing junction right to the washer or shim.
Bayonet thermocouples use a tube and wire design utilizing stranded thermocouple cable through out the probe. The metallic probe is made of 301, 304 or 316 series stainless steel. The thermocouple can made with a grounded, or ungrounded junction. A grounded junction is welded to the tip of the probe and, while it has very fast response, it can conduct electrical noise back to the instrumentation. An ungrounded junction is isolated from the metallic probe, and prevents electrical noise transmission. However, ungrounded junctions are slightly slower to respond to temperature changes.
For more information on plastics thermocouples, contact Duro-Sense by visiting https://duro-sense or by calling 310-533-6877.
Thursday, March 29, 2018
High Quality, Precision Temperature Sensors for Military and Aerospace Applications
Duro-Sense offers a wide selection of thermocouples and RTD's for the military and aerospace industries. All sensors are designed for high-reliability and to endure shock,
vibration, and widely-changing ambient environments. All products are calibrated to NIST standards and are ISO9001, AS9100, ISO17025 compliant. All temperature sensors are designed and tested to provide exceptional accuracy, stability and reliability in the most demanding environments.
Call 310-533-6877 of visit https://duro-sense.com for more information.
vibration, and widely-changing ambient environments. All products are calibrated to NIST standards and are ISO9001, AS9100, ISO17025 compliant. All temperature sensors are designed and tested to provide exceptional accuracy, stability and reliability in the most demanding environments.
Call 310-533-6877 of visit https://duro-sense.com for more information.
Monday, March 26, 2018
The 3 Most Common Temperature Sensors: Thermocouples, RTD's and Thermistors
This post explains the basic operation of the three most common temperature sensing elements - thermocouples, RTD's and thermistors.
A thermocouple is a temperature sensor that produces a micro-voltage from a phenomena called the Seebeck Effect. In simple terms, when the junction of two different (dissimilar) metals varies in temperature from a second junction (called the reference junction), a voltage is produced. When the reference junction temperature is known and maintained, the voltage produced by the sensing junction can be measured and directly applied to the change in the sensing junctions' temperature.
Thermocouples are widely used for industrial and commercial temperate control because they are inexpensive, fairly accurate, have a fairly linear temperature-to-signal output curve, come in many “types” (different metal alloys) for many different temperature ranges, and are easily interchangeable. They require no external power to work and can be used in continuous temperature measurement applications from -185 Deg. Celsius (Type T) up to 1700 Deg. Celsius (Type B).
Common application for thermocouples are industrial processes, the plastics industry, kilns, boilers, steel making, power generation, gas turbine exhaust and diesel engines, They also have many consumer uses such as temperature sensors in thermostats and flame sensors, and for consumer cooking and heating equipment.
RTD’s (resistance temperature detectors), are temperature sensors that measure a change in resistance as the temperature of the RTD changes. They are normally designed as a fine wire coiled around a bobbin (made of glass or ceramic), and inserted into a protective sheath. The can also be manufactured as a thin-film element with the pure metal deposited on a ceramic base much like a circuit on a circuit board.
The RTD wire is usually a pure metal such as platinum, nickel or copper because these metals have a predictable change in resistance as the temperature changes. RTD’s offer considerably higher accuracy and repeatability than thermocouples and can be used up to 600 Deg. Celsius. They are most often used in biomedical applications, semiconductor processing and industrial applications where accuracy is important. Because they are made of pure metals, they tend to more costly than thermocouples. RTD’s do need to be supplied an excitation voltage from the control circuitry as well.
The third most common temperature sensor is the thermistor. Thermistors work similarly to RTD’s in that they are a resistance measuring device, but instead of using pure metal, thermistors use a very inexpensive polymer or ceramic material as the element. The practical application difference between thermistors and RTD’s is the resistance curve of thermistors is very non-linear, making them useful only over a narrow temperature range.
Thermistors however are very inexpensive and have a very fast response. They also come in two varieties, positive temperature coefficient (PTC - resistance increases with increasing temperature), and negative temperature coefficient (NTC - resistance decreases with increasing temperature). Thermistors are used widely in monitoring temperature of circuit boards, digital thermostats, food processing, and consumer appliances.
For more information, contact Duro-Sense by calling 310-533-6877 or visit https://duro-sense.com.
![]() |
Thermocouple (image courtesy of Duro-Sense) |
Thermocouples are widely used for industrial and commercial temperate control because they are inexpensive, fairly accurate, have a fairly linear temperature-to-signal output curve, come in many “types” (different metal alloys) for many different temperature ranges, and are easily interchangeable. They require no external power to work and can be used in continuous temperature measurement applications from -185 Deg. Celsius (Type T) up to 1700 Deg. Celsius (Type B).
Common application for thermocouples are industrial processes, the plastics industry, kilns, boilers, steel making, power generation, gas turbine exhaust and diesel engines, They also have many consumer uses such as temperature sensors in thermostats and flame sensors, and for consumer cooking and heating equipment.
![]() |
Wire-wound RTD (image courtesy of Wikipedia) |
The RTD wire is usually a pure metal such as platinum, nickel or copper because these metals have a predictable change in resistance as the temperature changes. RTD’s offer considerably higher accuracy and repeatability than thermocouples and can be used up to 600 Deg. Celsius. They are most often used in biomedical applications, semiconductor processing and industrial applications where accuracy is important. Because they are made of pure metals, they tend to more costly than thermocouples. RTD’s do need to be supplied an excitation voltage from the control circuitry as well.
![]() |
Thermistor (image courtesy of Wikipedia) |
Thermistors however are very inexpensive and have a very fast response. They also come in two varieties, positive temperature coefficient (PTC - resistance increases with increasing temperature), and negative temperature coefficient (NTC - resistance decreases with increasing temperature). Thermistors are used widely in monitoring temperature of circuit boards, digital thermostats, food processing, and consumer appliances.
For more information, contact Duro-Sense by calling 310-533-6877 or visit https://duro-sense.com.
Subscribe to:
Posts (Atom)