Duro-Sense designs and manufactures temperature sensors and assemblies used in power generation, plastics production, semiconductor processing, environmental control, packaging, aerospace, medical equipment, foodservice equipment and a myriad of other industries. Duro-Sense partners with customers to optimize their temperature sensing processes, thereby assisting in improving their customers efficiency and profitability.
Since 1979, Duro-Sense has grown exponentially in product capability and market experience. The company today continues to succeed by operating under a simple core value – providing customers with superior products, meticulously engineered for their individual requirements.
A blog providing information about industrial temperature measurement, specifically in the areas of temperature sensors. The posts will contain educational information about thermocouples, RTDs, and other common types of temperature sensors. The application of these sensors will focus on aerospace, aircraft, research and development, medical, chemical, plastics processing, and power generation industries. For more, visit Duro-Sense.com or call 310-533-6877.
Showing posts with label RTD. Show all posts
Showing posts with label RTD. Show all posts
Friday, July 26, 2019
Thursday, July 11, 2019
Duro-Sense: A Long History of Solving Tough Temperature Sensing Problems

Duro-Sense offers their customers products and services designed to provide outstanding value and cost savings throughout the customer's equipment life span. By integrating the highest quality standards, state-of-the-art machinery, and decades of application experience, Duro-Sense assists customers through:
- Improved product quality
- Optimize asset uptime and performance
- Lower total cost of operation and maintenance
- Increase equipment reliability
- Improve plant and personnel safety
ENGINEERING AND TECHNICAL SERVICES
Technical Analysis — Duro-Sense can identify temperature sensor operational issues that may be constraining output or elevating operating costs, and then recommend laser-focused solutions.
Reliability and Efficiency Services — Duro-Sense lends their decades of hands-on experience to offer practical temperature sensing solutions that improve the performance, efficiency, and reliability of your process control equipment - all while lowering your total cost of ownership.
Loop Design, Integration and Engineering Support — Duro-Sense engineers engage with their customers, providing support for grassroots project planning, system design, or project management requirements.
Equipment Life Cycle Optimization — Through a combination of assessments and technology, Duro-Sense experts help customers benchmark operational performance, define key metrics, and implement precise sensor solutions to achieve long-term operational goals.
Intelligent Product Design — By employing an array of sophisticated products, services, and software that collects, examines and understands data, Duro-Sense helps customers use predictive analytics to take action and improve asset reliability and reduce downtime.
Have a challenging temperature sensing requirement? Call Duro-Sense.
Duro-Sense Corporation
310-533-6877
Friday, May 24, 2019
Quick Comparison of Temperature Sensors
Thermocouples are commonly used because of their simplicity, reliability, and relative low cost. They are self-powered and eliminate the need for a separate sensor power supply. Thermocouples are quite durable when selected for a given application appropriately. Thermocouples can also be used for applications with high temperatures.
Resistance temperature detectors (RTDs) are attractive alternatives to thermocouples when the output is desired to be highly accurate, stable and linear (i.e. just how close the calibration curve looks a straight line). The superior linearity of relative temperature resistance enables simpler signal processing devices for RTDs than thermocouples.
Thermistors are similar to RTD because they're a resistance measurement device, but thermistors use a very cheap polymer or ceramic material as the element in lieu of the use of pure metal.
For more information on any type of industrial or OEM temperature sensor, contact Duro-Sense by calling 310-533-6877 or by visiting https://duro-sense.com.
Labels:
industrial thermocouple,
OEM,
RTD,
temperature sensor,
thermistor,
thermocouple
Monday, March 25, 2019
A Pro and Con Comparison of Thermocouples and RTDs
Thermocouple Advantages
- Inexpensive
- Wide temperature range
- Various types, sizes and application methods
- Remote read back
- Read back electronics can be simple
- Usable in virtually any environment
- Requires cold junction compensation
- Slow response time
- Not as accurate as many other devices without good CJC and calibration
- Susceptible to noise
- Connection cable/wire is expensive compared to copper conductors
- Cable/wire length is limited
- More linear than thermocouples
- Cold junction not an issue
- Special cable/wire not needed
- Cable/wire length can be much longer than TC’s
- Better noise immunity
- More stable over time than thermocouples
- Remote read back
- Usable in virtually any environment
- More expensive than thermocouples
- More delicate than thermocouples unless encased
- Not as wide of temperature range as thermocouples
- Requires more conductors per device
- Read back electronics more complex
Tuesday, March 12, 2019
Theory of RTD Operation
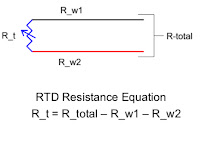
Most commonly used is the platinum 100 ohm RTD because of their stability in air and linearity. Their resistance is 100 ohms @ 0 Deg.C and increases with temperature.

Alpha is ohms per ohm per Deg.C.
The average resistance change per unit of temperature from boiling point to ice point of water:
- Rboiling – Rice point/100deg/100ohms
- 138.5 – 100.0/100/100 = .00385
Tolerance class is the amount an RTD will differ from the standard resistance curve per Deg.C.
- Class A (+/- .15 + .002*t)
- @ temp of 100DegC = +/- .35DegC
When ordering an RTD, a tolerance class will be part of the order, dependent on the application. IEC 751 stipulates that the RTD be marked with their nominal R0 value, their tolerance class, the wiring configuration and the temperature range.
![]() |
3-wire configuration |
- Pt100 / A / 3 / -100/+200 = Platinum 100 Ohm / Class A / 3-Wire / -100 to +200 Deg.C
![]() |
2-wire configuration |
Another configuration is a two wire RTD with a stand-alone loop. (Probably rarely used today).
Since the RTD is a resistance device, the resistance of the wires used to connect the RTD to the measurement meter introduces errors and must be known. This is the reason a third (or fourth), wire is used.
![]() |
3rd wire used to cancel wire error |
Then the meter reads the resistance of one of the common wires, the RTD, and the non-common wire to determine Rtotal
![]() |
Meter reading 2 common wires |

Rt = Rtotal – Rwire
Friday, February 15, 2019
Temperature Sensing IS Rocket Science
Duro-Sense Corporation provides the precision temperature sensors to the aerospace, aviation, and space industries. Duro-Sense engineers bring proven solutions to your most difficult problems. Their R&D department is staffed with some of the industry's most qualified people, working in the most modern facilities to help advance the state of the art in temperature measurement.
Monday, January 28, 2019
Where to Mount Industrial Temperature Transmitters?
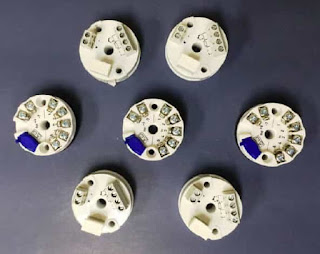
There are basically three different locations for the mounting of the temperature transmitters:
- In-head mounting - inside the connection head of the temperature sensors.
- Field mounting – close to the temperature sensors.
- Central mounting - in the vicinity of the control room
In-head mounting
The transmitters are mounted directly inside the connection head and are normally replacing the terminal block. This way of mounting normally offers the biggest advantages. It is however necessary to be aware of the environmental influence (mainly the temperature) on the measurement accuracy.Advantages
- Maximum safety in the signal transmission. The amplified signal, e.g. 4- 20 mA, is very insensitive to electrical disturbances being induced along the transmission cable.
- Cost savings for the transmission cables. Only two leads are required if a 2- wire transmitter is used.
- Cost savings for installation. No extra connection points because of the transmitter.
- Cost and space savings. No extra housings or cubicles are needed.
- Field instruments, e.g. indicators, can easily be installed, also at a later stage without redesigning the measuring circuits.
- The ambient temperatures can be out- side the allowed limits for the transmitters.
- The ambient temperature influence on the measuring accuracy has to be considered.
- Extreme vibrations might cause malfunction of the transmitters.
- The location of the temperature sensor can give maintenance problems.
Field mounting
The transmitters are either mounted directly beside the temperature sensors or in the vicinity of the sensors. Often more than one transmitter is mounted in the same field box.This method is more expensive than In-head mounting, but otherwise a good alternative offering most of the advantages of In-head mounting without the disadvantages mentioned above.
Advantages
- High safety in the signal transmission. The main part of the signal transmission is made with an amplified signal.
- No extreme temperatures or vibrations exist. This facilitates accurate and safe measurements.
- Cost savings for transmission cables.
- A wider selection of transmitters is available. DIN rail transmitters can also be used.Field instruments can often be installed easily.
- Maintenance can normally be carried out without problems.
- Higher installation costs compared to In-head mounting.
- Costs and space requirements for transmitter boxes or cubicles.
Central mounting
In this case, the transmitters are placed in the vicinity of the control room or in another central part of the plant They are often mounted inside cubicles, and/or closed rooms. The ambient conditions are normally very good and stable.This method offers the most convenient conditions for maintenance and the best possible environment for the transmitters. There are on the other hand some disadvantages that should be considered.
Advantages
- Convenient conditions for installation, commissioning and maintenance.
- Minimum risk for environmental influences (e.g. temperature influence).
- Reduced safety in the signal transmission. The low-level sensor signal is rather sensitive to electrical disturbances being induced along the trans- mission cable.
- Relatively high costs for cabling. T/C measurements require compensation or extension cables all the way to the transmitters. RTD measurements with high accuracy should be done in 4-wire connection to get rid of the lead resistance influence.
- Costs and space requirements for cubicles or frames.
- Rather complicated and expensive to connect field instruments, e.g. indicators.
For more information on using temperature transmitters, contact Duro-Sense by calling 310-533-6877 or by visiting https://duro-sense.com.
Wednesday, January 16, 2019
Tuesday, December 4, 2018
3 Bottom Line Criteria to Help You Choose Between Thermocouples and RTDs
Both RTD and thermocouple probes monitor temperature but which one is right for your application?
The first question to ask yourself is what is the temperature range you are trying to monitor?
Generally, if the temperature is above a hundred and fifty degrees Celsius, a thermocouple would be used. For anything below a hundred and fifty degrees Celsius, an RTD would be used.
The next question to ask is what is the required sensor accuracy?
RTDs provide more accurate readings with repeatable results, this is why RTDs are typically used when temperatures are within its monitoring range.
The last question is what is the purchase budget and how many do you need?
Thermocouples can be up to three times less expensive than RTD probes making thermocouples a good choice when purchasing a large quantity or when the budget is tight
These three criteria are VERY basic, and intended just to point you in the right direction. There are many other differences between thermocouples and RTDs that need to be understood before application. Always consult a temperature sensor application expert prior to installing or specifying a thermocouple or RTD where failure can cause harm.
Duro-Sense Corporation
https://duro-sense.com
The first question to ask yourself is what is the temperature range you are trying to monitor?
Generally, if the temperature is above a hundred and fifty degrees Celsius, a thermocouple would be used. For anything below a hundred and fifty degrees Celsius, an RTD would be used.
The next question to ask is what is the required sensor accuracy?
RTDs provide more accurate readings with repeatable results, this is why RTDs are typically used when temperatures are within its monitoring range.
The last question is what is the purchase budget and how many do you need?
Thermocouples can be up to three times less expensive than RTD probes making thermocouples a good choice when purchasing a large quantity or when the budget is tight
These three criteria are VERY basic, and intended just to point you in the right direction. There are many other differences between thermocouples and RTDs that need to be understood before application. Always consult a temperature sensor application expert prior to installing or specifying a thermocouple or RTD where failure can cause harm.
Duro-Sense Corporation
https://duro-sense.com
(310) 533-6877
Friday, November 9, 2018
Platinum Resistance Temperature Detectors
Platinum Resistance Thermometers Detectors (RTDs) rely on the fact that platinum, like many other metals, exhibits increased electrical resistance as temperature rises. For example, a conventional RTD designed to provide 100 Ohms at 0 °C has a resistance in the neighborhood of 80 Ohms at -50 °C and 120 Ohms at 50 °C, or a sensitivity of about 0.4 Ohms per degree. RTDs constructed to particularly exacting specifications, termed Standard Platinum Resistance Thermometers, are named as the defining measurement tools for interpolating temperatures under ITS-90. In general, RTDs can have high accuracy (0.01 °C), stability, and repeatability across a wide range of temperatures from -200 °C to 500 °C.
Typically the platinum element is formed into thick or thin films, or the platinum wire is arranged in two, three or four helical coils (see diagram, right) – the more coils, the higher the sensitivity. The film or wire is placed inside a glass or ceramic enclosure, and can be supported by loose or compacted MgO. Platinum-based leads connect the probe unit to the thermometer electronics, which convert the electrical signal to temperature.
RTDs are broadly divided into two groups: Industrial RTDs and Standard Platinum Resistance Thermometers, depending on sensitivity and robustness. ASTM and IEC define several classes of RTDs, each with a different set of specifications. An ASTM "Class A" unit, for example, has an out-of-the-box tolerance — maximum permissible error — that ranges from 0.47 °C at -200 °C to 0.13 °C at 0 °C to 0.98 °C at 500 °C.
Advantages
Disadvantages
Typically the platinum element is formed into thick or thin films, or the platinum wire is arranged in two, three or four helical coils (see diagram, right) – the more coils, the higher the sensitivity. The film or wire is placed inside a glass or ceramic enclosure, and can be supported by loose or compacted MgO. Platinum-based leads connect the probe unit to the thermometer electronics, which convert the electrical signal to temperature.
RTDs are broadly divided into two groups: Industrial RTDs and Standard Platinum Resistance Thermometers, depending on sensitivity and robustness. ASTM and IEC define several classes of RTDs, each with a different set of specifications. An ASTM "Class A" unit, for example, has an out-of-the-box tolerance — maximum permissible error — that ranges from 0.47 °C at -200 °C to 0.13 °C at 0 °C to 0.98 °C at 500 °C.
Advantages
- Wide temperature range
- Resistance-temperature relationship is well characterized.
- Rugged construction in industrial RTDs
- Available in different shapes and sizes – application specific
- Can be used with a digital temperature read-out device.
Disadvantages
- Mechanical shock and vibration will cause drift.
- Deterioration at elevated temperatures (e.g., >500 °C)
- 2-and 3-wire devices need lead-wire compensation.
- Non-hermetically sealed RTDs will deteriorate in environments with excessive moisture.
Post abstracted from "Mercury Thermometer Alternatives: Platinum Resistance Thermometers (PRTs)" by NIST.
Friday, September 28, 2018
Advantage and Disadvantages of Common Temperature Sensors
THERMOCOUPLE
![]() |
Thermocouple |
Thermocouple Advantages:
- Self-powered
- Simple
- Rugged
- Inexpensive
- Many applications
- Wide temperature range
- Fast response
- Nonlinear output signal
- Low voltage
- Reference required
- Accuracy is function of two separate measurements
- Least sensitive
- Sensor cannot be recalibrated
- Least stable
RTD
![]() |
RTD |
RTD Advantages:
- More stable at moderate temperatures
- High levels of accuracy
- Relatively linear output signal
- Expensive
- Self-heating
- Lower temperature range
THERMISTOR
![]() |
Thermistor |
Thermistor Advantages:
- High output
- Fast
- Two-wire ohms measurement
- Nonlinear
- Limited temperature range
- Fragile
- Current source required
- Self-heating
Sunday, September 23, 2018
Monday, September 10, 2018
Thermowells
![]() |
Thermowell (Duro-Sense) |
Thermowells may be made out of any material that is thermally conductive, pressure-tight, and not chemically reactive with the process. Most thermowells are formed out of either metal (stainless steel or other alloy) or ceramic materials. A simple diagram showing a thermowell in use with a temperature sensor (RTD) is shown here:
As useful as thermowells are, they are not without their caveats. All thermowells, no matter how well they may be installed, increase the first-order time lag of the temperature sensor by virtue of their mass and specific heat value. It should be intuitively obvious that a few pounds of metal will not heat up and cool down as fast as a few ounces’ worth of RTD or thermocouple, and therefore the addition of a thermowell to the sensing element will decrease the responsiveness of any temperature- sensing element. What is not so obvious is that such time lags, if severe enough, may compromise the stability of feedback control. A control system receiving a “delayed” temperature measurement will not see the live temperature of the process in real time due to this lag.
![]() |
RTD with Thermowell |
Reprinted from Lessons In Industrial Instrumentation by Tony R. Kuphaldt – under the terms and conditions of the Creative Commons Attribution 4.0 International Public License.
Tuesday, August 28, 2018
Temperature Transmitters
![]() |
Temperature Transmitters (Duro-Sense) |
Analog Transmitters: These transmitters are designed on analog circuit technology. They normally offer basic functions such as temperature linearization and sensor break technology. Sometimes they are adjustable for different measuring ranges, often with a fast response time.
Digital Transmitters: This transmitter type is mainly based on a microprocessor. They are often called intelligent transmitters, because they normally offer many extra features, which are not possible to realize in analog transmitters.
In-Head Transmitters: These transmitters are designed for mounting in the connection heads of temperature sensors. All Duro-Sense in-head transmitters fit into DIN B heads or larger. Special care has to be devoted to the ruggedness because of the harsh conditions that sometimes exist.
DIN Rail Transmitters: DIN rail transmitters are designed to be snapped onto a DIN rail. Duro-Sense DIN rail transmitters fit on a 35mm rail according to DIN EN 50022.
RTD Transmitters: RTD transmitters are used only for RTD sensors. (Pt100, Pt1000, Ni100, etc.). Normally they can handle only one RTD type. Most Duro-Sense transmitters can handle more than one type of RTD and are either fix- ranged or adjustable. They all have linear output.

Analog Output: The output signal is a current (4-20mA). Some transmitters are available with 0-20mA or 0-10mA output. The signal is normally proportional to the measured value within a defined measurement range.
Digital Output: The measured value (temperature) is presented as a binary coded message. So called Fieldbus transmitters use this technique. The Fieldbus transmitters on the market today use different standards for the communication thus creating some problems when integrating them with other instrumentation. Examples of standard available are: PROFIBUS, Interbus, Foundation Fieldbus, LonWorks and CAN-bus.
Analog and Digital Output: The HART transmitters have an analog output with a superimposed digital signal on the same wires. Typically, the analog signal is used for normal measurements and the digital signal only for temporary measurements, because of the low communication speed. The digital signal is mainly used for configuration and status information.
Isolated Transmitters: Isolated transmitters have no leading connections between circuits that are isolated from each other. The isolation effectively eliminates the risk for circulating currents and facilitates the connection of transmitters to control systems with grounded inputs.
Non-Isolated Transmitters: These transmitters have leading connections between, for instance, input and output circuits. They should be used with care.
For more information on temperature transmitters, visit https://duro-sense.com or call 310-533-6877.
Friday, August 17, 2018
Temperature Sensors for the Toughest Applications
![]() |
Click for larger view. |
All Duro-Sense customers benefit from years of tackling difficult applications. By implementing stringent quality practices and advanced manufacturing processes, Duro-Sense continues to solve the most challenging temperature sensing applications.
Duro-Sense is a one-stop, full service provider of anything related to temperature sensing. Service. Quality. On-time delivery.
Rely on the Duro-Sense difference.
www.duro-sense.com | 310-533-6877.
Friday, August 3, 2018
Video: Comparison of Thermocouples and RTDs
The video below describes the basic differences between industrial thermocouples and RTDs.
Duro-Sense Corporation provides the thermocouples, RTDs, thermowells, and accessories to the aerospace, aviation, process control, medical, R&D, power generation, alternative energy, plastics, primary metals, high-tech and OEM industries.
https://duro-sense.com
310-533-6877
Duro-Sense Corporation provides the thermocouples, RTDs, thermowells, and accessories to the aerospace, aviation, process control, medical, R&D, power generation, alternative energy, plastics, primary metals, high-tech and OEM industries.
https://duro-sense.com
310-533-6877
Friday, July 6, 2018
Common Terminology Used in Temperature Measurement and Process Control
Accuracy: The closeness of an indicator or reading of a measurement device to the actual value of the quantity being measured; usually expressed as ± percent of the full scale output or reading.
Drift: The change in output or set point value over long periods of time due to such factors as temperature, voltage, and time.
Hysteresis: The difference in output after a full cycle in which the input value approaches the reference point (conditions) with increasing, then decreasing values or vice versa; it is measured by decreasing the input to one extreme (minimum or maximum value), then to the other extreme, then returning the input to the reference (starting) value.
Linearity: How closely the output of a sensor approximates a straight line when the applied input is linear.
Noise: An unwanted electrical interference on signal wires.
Nonlinearity: The difference between the actual deflection curve of a unit and a straight line drawn between the upper and lower range terminal values of the deflection, expressed as a percentage of full range deflection.
Precision: The degree of agreement between a number of independent observations of the same physical quantity obtained under the same conditions.
Repeatability: The ability of a sensor to reproduce output readings when the same input value is applied to it consecutively under the same conditions.
Resolution: The smallest detectable increment of measurement.
RTD: Abbreviation for "resistance temperature detector". Resistance temperature detectors are temperature sensors that are widely used because of their high accuracy, stability, and linearity. They work on the principle that the resistivity of metals is dependent upon temperature; as temperature increases, resistance increases. Resistance Temperature Detector’s can withstand temperatures up to approximately 800 C (~1500 F).
Sensitivity: The minimum change in input signal to which an instrument can respond. Stability: The ability of an instrument to provide consistent output over an extended
period during which a constant input is applied.
Thermocouple: A temperature sensing device widely used because they are relatively low cost, self-powered, durable and capable sensing high temperatures. Thermocouples generate and micro voltage in relation to temperature change.
Zero balance: The ability of the transducer to output a value of zero at the electronic null
point.
Drift: The change in output or set point value over long periods of time due to such factors as temperature, voltage, and time.
Hysteresis: The difference in output after a full cycle in which the input value approaches the reference point (conditions) with increasing, then decreasing values or vice versa; it is measured by decreasing the input to one extreme (minimum or maximum value), then to the other extreme, then returning the input to the reference (starting) value.
Linearity: How closely the output of a sensor approximates a straight line when the applied input is linear.
Noise: An unwanted electrical interference on signal wires.
Nonlinearity: The difference between the actual deflection curve of a unit and a straight line drawn between the upper and lower range terminal values of the deflection, expressed as a percentage of full range deflection.
Precision: The degree of agreement between a number of independent observations of the same physical quantity obtained under the same conditions.
Repeatability: The ability of a sensor to reproduce output readings when the same input value is applied to it consecutively under the same conditions.
Resolution: The smallest detectable increment of measurement.
RTD: Abbreviation for "resistance temperature detector". Resistance temperature detectors are temperature sensors that are widely used because of their high accuracy, stability, and linearity. They work on the principle that the resistivity of metals is dependent upon temperature; as temperature increases, resistance increases. Resistance Temperature Detector’s can withstand temperatures up to approximately 800 C (~1500 F).
Sensitivity: The minimum change in input signal to which an instrument can respond. Stability: The ability of an instrument to provide consistent output over an extended
period during which a constant input is applied.
Thermocouple: A temperature sensing device widely used because they are relatively low cost, self-powered, durable and capable sensing high temperatures. Thermocouples generate and micro voltage in relation to temperature change.
Zero balance: The ability of the transducer to output a value of zero at the electronic null
point.
Friday, June 8, 2018
Precision RTD's (Resistance Temperature Detectors)
Duro-Sense RTDs, thermowells, and accessories provide high quality solutions to the aerospace, aviation, process control, medical, R&D, power generation, alternative energy, plastics, primary metals, high-tech and OEM industries.
https://duro-sense.com
310-533-6877
https://duro-sense.com
310-533-6877
Friday, May 25, 2018
Power Plant Temperature Sensors
Power plants (generating facilities) transform the mechanical energy of a spinning generator into electrical energy. Heat (from flame, nuclear reaction, or chemical reaction) is used to create steam that, in turn, produces the mechanical energy to drive turbines. There are many areas where precision temperature measurement and monitoring is critical to keep power plant systems running. Thermocouples and RTD sensors provide accurate, repeatable, and reliable measurement.
Duro-Sense
https://duro-sense.com
Phone: 310-533-6877
Duro-Sense
https://duro-sense.com
Phone: 310-533-6877
Labels:
Duro-Sense,
industrial thermocouple,
power generation,
power plant,
powergen,
RTD
Wednesday, May 16, 2018
RTD and Thermocouple Selection and Location for Optimal Control
![]() |
Loop diagram * |
Most temperature control loops have (5) four major components:
1) The media to be heated (e.g. metal platen, a tank of liquid, a stream of gas)
2) A energy source (e.g. electric heater, steam, hot oil, flame)
3) A temperature sensor (thermocouple, RTD)
4) A controller (e.g. electronic thermostat, PID controller)
5) Control element (e.g. control valve, SCR, SSR)
Temperature controllers provide sophisticated functions that "learn" or understand the relationship between available power and sensor temperature. They then adjust the amount of energy (heat) added, based on the current reading of the sensor and the desired temperature setpoint. Unfortunately, temperature controllers are often relied upon to overcome the oversights and inadequacies of poor control loop design.
![]() |
Lag time * |
In the most ideal situation, temperature sensors, the energy source and process media would all be at the same physical location. Since it's virtually impossible to accomplish this, compromises have to be made to allow for the mechanical, physical, and electrical realities of the application. Here are some practical recommendations for sensor selection and placement to improve temperature loop performance:
- Thermocouples, because of their low mass generally have a response advantage over RTDs.
- Exposed junction thermocouples are the fastest responding (least lag) sensor choice, but they are also the most prone to physical and chemical damage.
- Narrow, sheathed, grounded junction magnesium oxide insulated thermocouples are nearly as fast as exposed junctions, and provide protection from the process media.
- Applications that require protection sheaths and thermowells for RTDs and thermocouples increase sensor lag time.
- An immersion length of at least 10 times the diameter of the thermowell or sensor sheath should be used to minimize heat loss along the sensor sheath or thermowell wall from tip to process connection.
- Where possible, insert the temperature sensor in a pipe elbow into the oncoming flow.
- Tapered, swaged, or stepped thermowells are faster responding
- Always make sure the fit between sensor outer diameter and thermowell inner diameter is tight, and that the tip of the sensor is in direct contact with the thermowell.
* Images courtesy of Tony Kuphaldt and his book "Lessons In Industrial Instrumentation"
Subscribe to:
Posts (Atom)